Flame-retardant PVC (polyvinyl chloride) composite material for refrigerator back plate and preparation method of flame-retardant PVC composite material
A composite material and flame retardant technology, which is applied in the field of flame retardant PVC composite materials for refrigerator backplanes and their preparation, can solve the problem that the flame retardant effect can only reach UL94-V1 level, and can solve the problem that the strength is greatly reduced, Good resistance to deformation and the effect of preventing the spread of fire
- Summary
- Abstract
- Description
- Claims
- Application Information
AI Technical Summary
Problems solved by technology
Method used
Image
Examples
Embodiment 1
[0049]
[0050]
[0051] Among them, the acrylate copolymer is copolymerized by methyl methacrylate and vinyl acetate with a weight ratio of 60:40, and the number average molecular weight is 2.6×10 4 .
[0052] The above-mentioned raw materials are added to the high-speed mixer according to the ratio, and the temperature is raised to 110 ° C and mixed for 10 minutes at a rotating speed of 500 r / min. Then, the extruder is used for extrusion molding. 175°C, 170°C in the metering section, and 170°C in the machine head to obtain a PVC composite material.
Embodiment 2
[0054]
[0055] Among them, the acrylate copolymer is copolymerized by methyl methacrylate and vinyl acetate with a weight ratio of 50:50, and the number average molecular weight is 3.0×10 4 .
[0056] The above-mentioned raw materials are added to the high-speed mixer according to the ratio, and the temperature is raised to 100 ° C and mixed for 10 minutes at a rotating speed of 500 r / min. Then, the extruder is used for extrusion molding. 175°C, 170°C in the metering section, and 170°C in the machine head to obtain a PVC composite material.
Embodiment 3
[0058]
[0059]
[0060] Among them, the acrylate copolymer is copolymerized by methyl methacrylate and vinyl acetate with a weight ratio of 70:30, and the number average molecular weight is 2.8×10 4 .
[0061] The above-mentioned raw materials are added to the high-speed mixer according to the ratio, and the temperature is raised to 100 ° C and mixed for 10 minutes at a rotating speed of 500 r / min. Then, the extruder is used for extrusion molding. 175°C, 170°C in the metering section, and 170°C in the machine head to obtain a PVC composite material.
PUM
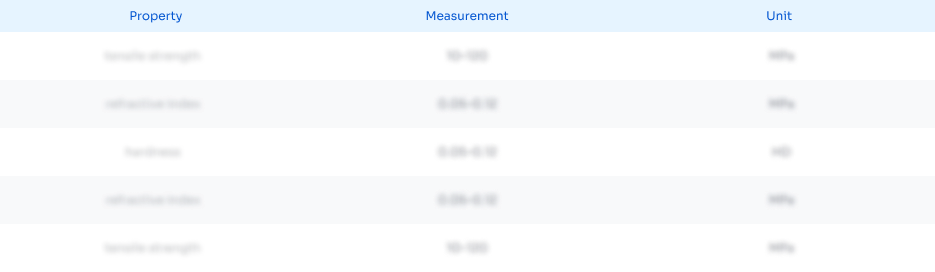
Abstract
Description
Claims
Application Information

- Generate Ideas
- Intellectual Property
- Life Sciences
- Materials
- Tech Scout
- Unparalleled Data Quality
- Higher Quality Content
- 60% Fewer Hallucinations
Browse by: Latest US Patents, China's latest patents, Technical Efficacy Thesaurus, Application Domain, Technology Topic, Popular Technical Reports.
© 2025 PatSnap. All rights reserved.Legal|Privacy policy|Modern Slavery Act Transparency Statement|Sitemap|About US| Contact US: help@patsnap.com