Heat-conducting BOPP (Biaxially-oriented Polypropylene) film
A film and film preparation technology, applied in the direction of coating, polyurea/polyurethane coating, etc., can solve problems such as structural defects, limited improvement of thermal conductivity, mechanical properties that cannot meet the requirements, etc., to achieve increased viscosity, avoid interface separation, and heat conduction good performance
- Summary
- Abstract
- Description
- Claims
- Application Information
AI Technical Summary
Problems solved by technology
Method used
Image
Examples
Embodiment 1
[0026] A method for preparing a thermally conductive BOPP film, comprising the following steps:
[0027] S1, mix 10kg of ethanol, 1kg of polyvinylpyrrolidone, and 5kg of water evenly, add 1kg of graphene, ultrasonically peel for 1h, centrifuge for 2min at a speed of 10000r / min, take the supernatant, add 1kg of 4,4-diaminodiphenyl Ether and 1kg of pyromellitic dianhydride were reacted for 1h, and 1kg of water-based polyurethane was added to disperse evenly to obtain a graphene / polyurethane composite dispersion;
[0028] S2. The BOPP membrane was cleaned with deionized water and acetone to remove surface impurities, dried and immersed in an aqueous solution of ammonium persulfate with a mass fraction of 10%, and irradiated with a UV high-pressure mercury lamp for 2 minutes with a light intensity of 8000 μw / cm 2 , λ is 254nm, and then immersed in water at 30°C for 1min to obtain a surface-activated BOPP film;
[0029] S3. The graphene / polyurethane composite dispersion is spin-co...
Embodiment 2
[0031] A method for preparing a thermally conductive BOPP film, comprising the following steps:
[0032] S1, mix 20kg ethanol, 3kg polyvinylpyrrolidone, and 15kg water evenly, add 5kg graphene, ultrasonically peel for 2h, centrifuge 5min at a speed of 12000r / min, get the supernatant, add 3kg 4,4-diaminodiphenyl Ether and 2kg of pyromellitic dianhydride were reacted for 2h, and 5kg of water-based polyurethane was added to disperse evenly to obtain a graphene / polyurethane composite dispersion;
[0033] S2. The BOPP membrane was washed with deionized water and acetone to remove surface impurities, dried and immersed in an aqueous solution of ammonium persulfate with a mass fraction of 16%, and irradiated with ultraviolet high-pressure mercury lamp for 6 minutes, and the light intensity was 9000 μw / cm 2 , λ is 254nm, and then immersed in water at 50°C for 2min to obtain a surface-activated BOPP film;
[0034] S3. The graphene / polyurethane composite dispersion is spin-coated on th...
Embodiment 3
[0036] A method for preparing a thermally conductive BOPP film, comprising the following steps:
[0037] S1, mix 13kg of ethanol, 2.5kg of polyvinylpyrrolidone and 8kg of water, add 4kg of graphene, ultrasonically peel for 70min, centrifuge for 3min at a speed of 11500r / min, take the supernatant, add 2.5kg of 4,4-diamino Diphenyl ether and 1.3kg of pyromellitic dianhydride were reacted for 110min, and 2kg of water-based polyurethane was added for uniform dispersion to obtain graphene / polyurethane composite dispersion;
[0038] S2. The BOPP membrane was cleaned with deionized water and acetone to remove surface impurities, dried and immersed in an aqueous solution of ammonium persulfate with a mass fraction of 14%, and irradiated with ultraviolet high-pressure mercury lamp for 3 minutes, and the light intensity was 8800 μw / cm 2 , λ is 254nm, and then immersed in water at 35°C for 1.7min to obtain a surface-activated BOPP film;
[0039] S3. The graphene / polyurethane composite d...
PUM
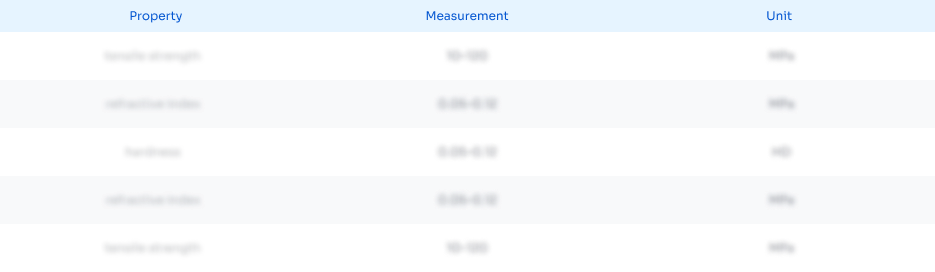
Abstract
Description
Claims
Application Information

- R&D Engineer
- R&D Manager
- IP Professional
- Industry Leading Data Capabilities
- Powerful AI technology
- Patent DNA Extraction
Browse by: Latest US Patents, China's latest patents, Technical Efficacy Thesaurus, Application Domain, Technology Topic, Popular Technical Reports.
© 2024 PatSnap. All rights reserved.Legal|Privacy policy|Modern Slavery Act Transparency Statement|Sitemap|About US| Contact US: help@patsnap.com