Modular underwater pile foundation structure self-adaptive cleaning and damage detection mechanical arm
A damage detection and modular technology, applied in the field of manipulators, can solve problems such as unreasonable solutions to engineering problems, functional limitations, and unfavorable practice, and achieve the effects of reducing equipment adjustment costs, improving operation safety, and reducing labor costs.
- Summary
- Abstract
- Description
- Claims
- Application Information
AI Technical Summary
Problems solved by technology
Method used
Image
Examples
Embodiment 1
[0028] like Figure 1-5 As shown, this embodiment provides a modular underwater pile foundation structure self-adaptive cleaning and damage detection robot arm, which includes a transmission arm rod 2, one end of the transmission arm rod 2 is provided with a modular interface 1, and the other side of the transmission arm rod 2 is provided. One end is provided with a robotic arm connecting portion 3, and two arm frames 100 are respectively provided on the robotic arm connecting portion 3. Any arm frame 100 includes an inner arm frame 4 and an outer arm frame 5, and an inner arm frame 4 and an outer arm frame 5. Connected by the joint 41, the inner side of the arm frame 100 is provided with a software moving cleaning part 6;
[0029] The modular interface 1 is connected to the underwater drone interface to transmit current and control signals. The built-in waterproof steering gear of the transmission arm rod 2 receives the control signal and drives the mechanical arm connecting ...
PUM
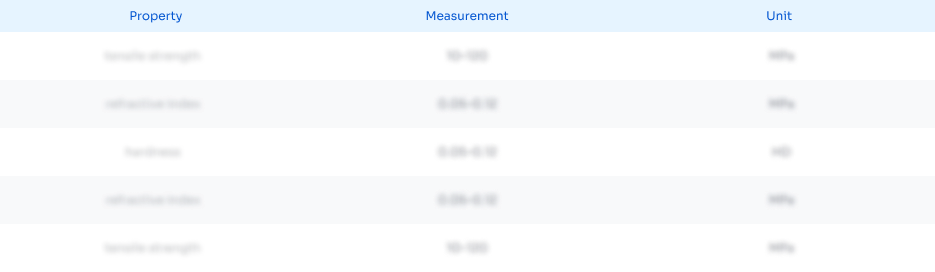
Abstract
Description
Claims
Application Information

- Generate Ideas
- Intellectual Property
- Life Sciences
- Materials
- Tech Scout
- Unparalleled Data Quality
- Higher Quality Content
- 60% Fewer Hallucinations
Browse by: Latest US Patents, China's latest patents, Technical Efficacy Thesaurus, Application Domain, Technology Topic, Popular Technical Reports.
© 2025 PatSnap. All rights reserved.Legal|Privacy policy|Modern Slavery Act Transparency Statement|Sitemap|About US| Contact US: help@patsnap.com