Low-carbon additive supporting structure construction device, heading machine and construction method
A support structure and roadheader technology, which is applied in shaft equipment, earthwork drilling, shaft lining, etc., can solve problems such as synchronous support for tunnels, and achieve the effects of avoiding construction risks, ensuring structural quality, and fast construction speed
- Summary
- Abstract
- Description
- Claims
- Application Information
AI Technical Summary
Problems solved by technology
Method used
Image
Examples
Embodiment 2
[0035] Example 2, which differs from Example 1 in that, as image 3 As shown, the fabric output mechanism 1 includes a fabric output housing 15, and the end of the fabric output housing 15 facing the rock wall 10 is provided with a fabric output port 12 for outputting the fabric 11 and a fabric rolling member for rolling the fabric 11 13. The other end of the fabric output housing 15 is fixed to the fabric output housing 15, and the fabric rolling element 13 rolls and adheres the fabric 11 output from the fabric output port 12 to the rock wall 10.
Embodiment 3
[0036] Example 3, the difference from Example 2 is that, as image 3 As shown, the end of the fabric output housing 15 close to the fabric output port 12 facing the rock wall 10 is provided with a nozzle 14 for spraying the adhesive, and the nozzle 14, the fabric output port 12 and the fabric rolling member 13 drive along the The rotation directions of the device 7 are set in sequence, so that after the nozzle 14 sprays the adhesive to the rock wall 10 , the fabric 11 is rolled on the rock wall 10 by the fabric rolling member 13 . Wherein, the fabric 11 is a flexible fabric. In this implementation, the binder is stored in the rear matching 9 , and the roadheader is provided with a pipeline and a pump for transporting the binder stored in the rear matching 9 to the spout 14 .
Embodiment 4
[0037] Example 4, the difference from Example 1 is that, as Figure 4 As shown, the reinforced material output mechanism 2 includes a reinforced material output casing 24, and one end of the reinforced material output casing 24 facing the rock wall 10 is provided with a reinforced material output port 22 for outputting the reinforced material 21 and a reinforced material output port 22 for rolling the reinforced material. 21, the other end of the reinforcement output housing 24 is fixed with the fabric output housing 15, and the reinforcement rolling piece 23 rolls the reinforcement 21 output from the reinforcement output port 22 to fit the fabric output. On the fabric 11 applied by the mechanism 1 . Wherein, the rib material 21 is a mesh-shaped or strip-shaped rib-shaped web. The pores of the rib material roll net allow the large particle components in the adhesive material 31 to pass through, ensuring that the adhesive material 31 does not segregate and evenly covers the ri...
PUM
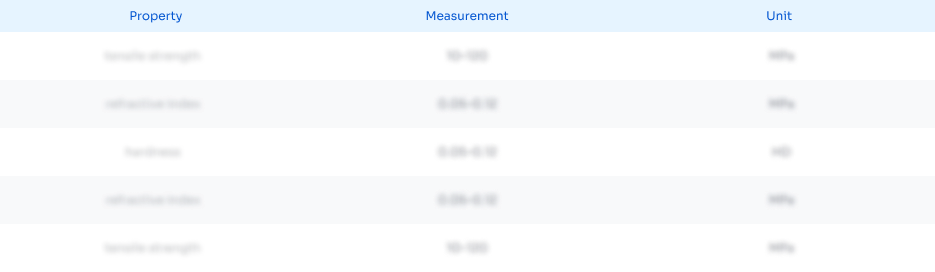
Abstract
Description
Claims
Application Information

- Generate Ideas
- Intellectual Property
- Life Sciences
- Materials
- Tech Scout
- Unparalleled Data Quality
- Higher Quality Content
- 60% Fewer Hallucinations
Browse by: Latest US Patents, China's latest patents, Technical Efficacy Thesaurus, Application Domain, Technology Topic, Popular Technical Reports.
© 2025 PatSnap. All rights reserved.Legal|Privacy policy|Modern Slavery Act Transparency Statement|Sitemap|About US| Contact US: help@patsnap.com