Extrusion forming equipment for processing nano sponge composite acoustic panel and production process
A nano-sponge and extrusion molding technology, which is applied in the field of processing equipment for nano-sponge composite sound-absorbing panels, can solve troubles and other problems
- Summary
- Abstract
- Description
- Claims
- Application Information
AI Technical Summary
Problems solved by technology
Method used
Image
Examples
Embodiment 1
[0031] Example 1, as Figure 1-8 As shown, the present invention provides an extrusion molding equipment for processing nano-sponge composite sound-absorbing panels, including a main body 1 and a pushing device 7, the main body 1 is an extrusion molding machine, and a connecting block 2 is fixedly connected to one side of the main body 1.
[0032] The specific settings and functions of the pushing device 7 , the fixing device 8 and the storage device 9 will be described in detail below.
[0033] like image 3 and Figure 4 As shown, the side of the connection block 2 away from the main body 1 is provided with a wire 4, the end of the wire 4 away from the connection block 2 is provided with a tray 5, one end of the tray 5 is fixedly connected with a support column 6, and the inner wall of the main body 1 is fixedly connected with a mold 3 , first pour the sound-absorbing plate blank into the mold 3, and then extrude the sound-absorbing plate through the body 1, and then turn ...
Embodiment 2
[0037] Embodiment 2, on the basis of Embodiment 1, the side of the main body 1 away from the connection block 2 is provided with a storage device 9, the storage device 9 includes a placement plate 95, one end of the placement plate 95 is fixedly connected to the body 1, and the placement plate 95 In the shape of "L", first place the processed sound-absorbing panel on the placing plate 95, and then pull the limit block 93 to make the limit block 93 slide inside the placing plate 95, so that the limit block 93 is not in phase with the sliding plate 92. contact, so that the third spring 94 pulls the sliding plate 92 due to the recovery of the elastic force, so that the sliding plate 92 slides on the inner wall of the chute 96. At this time, the sliding plate 92 will be in contact with the sound-absorbing plate, so that the sound-absorbing plate is fixed by the pressure of the sliding plate 92 On the placing plate 95, a limit block 93 is inserted through one side of the placing pla...
PUM
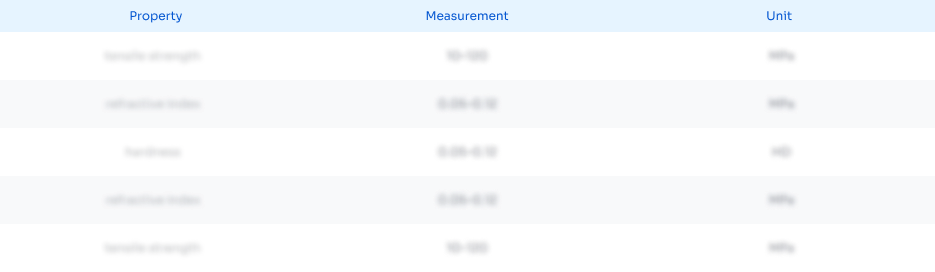
Abstract
Description
Claims
Application Information

- Generate Ideas
- Intellectual Property
- Life Sciences
- Materials
- Tech Scout
- Unparalleled Data Quality
- Higher Quality Content
- 60% Fewer Hallucinations
Browse by: Latest US Patents, China's latest patents, Technical Efficacy Thesaurus, Application Domain, Technology Topic, Popular Technical Reports.
© 2025 PatSnap. All rights reserved.Legal|Privacy policy|Modern Slavery Act Transparency Statement|Sitemap|About US| Contact US: help@patsnap.com