Forming method of sheet metal component with composite characteristics of bulge rib and groove
A compound feature and bulging technology, applied in the field of sheet metal forming processing, can solve problems such as poor forming quality, achieve high pass rate, improve overall forming quality, and facilitate control
- Summary
- Abstract
- Description
- Claims
- Application Information
AI Technical Summary
Problems solved by technology
Method used
Image
Examples
Embodiment 1
[0056] refer to Figure 1-Figure 13 , this embodiment provides a method for forming a sheet metal component with a composite feature of bulging ribs and grooves, including the following steps:
[0057] The first die is used to carry out the first stamping and deep drawing of the part, so as to form the bulge area 1 of the part and the overall profile of the web; wherein, the direction of the first stamping and deep drawing is the vertical line between the part's web and the bulge. line direction;
[0058] The second die is used to carry out the second stamping and deep drawing of the part to form the rib groove area 2 of the part; wherein, the bulge of the part is placed downward, and the direction of the second stamping and drawing is the same as that of the first stamping and drawing. The deep direction is the same.
[0059] Since the current forming of complex sheet metal parts for the composite features of such bulging ribs and grooves mainly relies on the drop hammer pr...
Embodiment 2
[0105] refer to Figure 4-Figure 13 , this embodiment provides a method for forming a sheet metal component with a composite feature of bulging ribs and grooves, including the following steps:
[0106] Using two-pass stamping and deep drawing, the bulge area 1 and the web profile of the first forming part are formed with the bulge facing up, and the rib groove area 2 of the second forming part, the bulge area is facing down;
[0107] When designing the mold, the first mold is provided with an exhaust hole 15 in the non-working area of the bulge, and a storage bulge in the web area. Taking 4 cavities as an example, the original size of the cavity is:
[0108] 1) The dimensions of the two cavities near the bulge area 1 are: L 1 =202mm, L 2 =185mm, B 1 =126mm, B 2 =114mm, H=14mm;
[0109] 2) The dimensions of the two cavities away from the bulge area 1 are: L 1 =252mm, L 2 = 237mm, B 1 =134mm, B 2 =118mm, H=14mm;
[0110] The dimensions of the design storage drum are ...
PUM
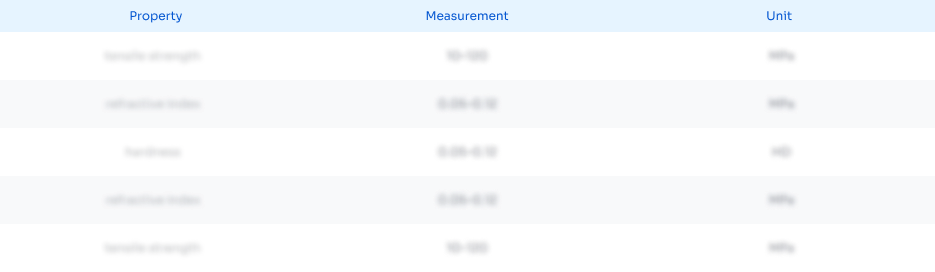
Abstract
Description
Claims
Application Information

- Generate Ideas
- Intellectual Property
- Life Sciences
- Materials
- Tech Scout
- Unparalleled Data Quality
- Higher Quality Content
- 60% Fewer Hallucinations
Browse by: Latest US Patents, China's latest patents, Technical Efficacy Thesaurus, Application Domain, Technology Topic, Popular Technical Reports.
© 2025 PatSnap. All rights reserved.Legal|Privacy policy|Modern Slavery Act Transparency Statement|Sitemap|About US| Contact US: help@patsnap.com