Wear-resistant textile fabric and preparation method thereof
A textile fabric and wear-resistant technology, applied in the field of textile fabrics, can solve the problems of heavy, uncomfortable, and not too soft canvas, and achieve the effects of excellent wear resistance, excellent high strength, and excellent moisture resistance.
- Summary
- Abstract
- Description
- Claims
- Application Information
AI Technical Summary
Problems solved by technology
Method used
Image
Examples
Embodiment 1
[0025] The composite nylon fiber comprises the following steps:
[0026] Add zirconium oxychloride to phosphoric acid solution with a concentration of 10 mol / L, stir at a constant speed for 30 min to obtain a mixed solution, transfer the mixed solution to a reaction kettle, heat up to 200 ° C, reflux for 24 h, and cool to room temperature after the reaction is completed, The supernatant was removed, centrifuged, and the solid product was washed with deionized water until the filtrate was neutral, then vacuum-dried and ground to obtain precursor particles, and the dosage ratio of zirconium oxychloride and phosphoric acid solution was controlled to be 30g:350mL;
[0027] Disperse the precursor particles in deionized water, maintain the system temperature at 0 °C, stir at a constant speed for 30 minutes, add a 30% mass fraction of tetrabutylammonium hydroxide aqueous solution, stir magnetically and react for 2 hours, then slowly add phosphoric acid dropwise, and continue to stir f...
Embodiment 2
[0031] The composite nylon fiber comprises the following steps:
[0032] The zirconium oxychloride was added to the phosphoric acid solution with a concentration of 10 mol / L, stirred at a constant speed for 30 min to obtain a mixed solution, transferred to the reaction kettle, heated to 200 ° C, refluxed for 24 hours, cooled to room temperature after the reaction, and cooled to room temperature. The supernatant was removed, centrifuged, and the solid product was washed with deionized water until the filtrate was neutral, then vacuum-dried and ground to obtain precursor particles, and the dosage ratio of zirconium oxychloride and phosphoric acid solution was controlled to be 32 g: 350 mL;
[0033]Disperse the precursor particles in deionized water, maintain the system temperature at 3 °C, stir at a constant speed for 30 minutes, add 30% mass fraction of tetrabutylammonium hydroxide aqueous solution, stir magnetically and react for 2 hours, then slowly add phosphoric acid dropwis...
Embodiment 3
[0037] The composite nylon fiber comprises the following steps:
[0038] Add zirconium oxychloride to phosphoric acid solution with a concentration of 10 mol / L, stir at a constant speed for 30 min to obtain a mixed solution, transfer the mixed solution to a reaction kettle, heat up to 200 ° C, reflux for 24 h, and cool to room temperature after the reaction is completed, The supernatant was removed, centrifuged, and the solid product was washed with deionized water until the filtrate was neutral, then vacuum-dried and ground to obtain precursor particles, and the dosage ratio of zirconium oxychloride and phosphoric acid solution was controlled to be 35g:350mL;
[0039] Disperse the precursor particles in deionized water, maintain the system temperature at 5 °C, stir at a constant speed for 30 minutes, add a 30% mass fraction of tetrabutylammonium hydroxide aqueous solution, stir magnetically and react for 2 hours, then slowly add phosphoric acid dropwise, and continue stirring ...
PUM
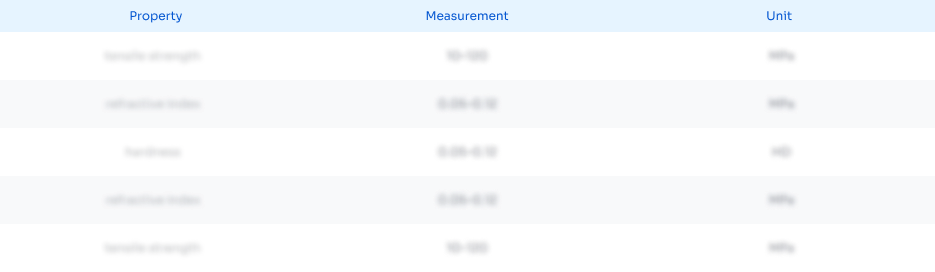
Abstract
Description
Claims
Application Information

- R&D Engineer
- R&D Manager
- IP Professional
- Industry Leading Data Capabilities
- Powerful AI technology
- Patent DNA Extraction
Browse by: Latest US Patents, China's latest patents, Technical Efficacy Thesaurus, Application Domain, Technology Topic, Popular Technical Reports.
© 2024 PatSnap. All rights reserved.Legal|Privacy policy|Modern Slavery Act Transparency Statement|Sitemap|About US| Contact US: help@patsnap.com