Natural rubber emulsion modified bamboo particle/magnesium oxychloride composite material and preparation method thereof
A technology of natural rubber latex and composite material, applied in the field of composite material preparation, can solve the problems of synthetic polymer material being difficult to decompose, environmental pollution, unable to take into account multiple properties at the same time, etc., to improve mechanical properties and water resistance, delay initial setting The effect of time and mechanical properties improvement
- Summary
- Abstract
- Description
- Claims
- Application Information
AI Technical Summary
Problems solved by technology
Method used
Image
Examples
Embodiment 1
[0037] A preparation method of natural rubber emulsion modified bamboo scraps / magnesium oxychloride composite material of the present invention, the amount of raw materials added is in parts by mass, comprising the following steps:
[0038] (1) Screening 70-mesh bamboo scraps and drying to a moisture content of 10%.
[0039] (2) adding 0.1 part of sodium lauryl sulfate to 1.8 parts of natural rubber latex, stirring evenly, and leaving for 5 days to fully react to obtain a modified natural rubber latex.
[0040] (3) Under normal temperature and pressure, 240.35 parts of magnesium chloride, 300.78 parts of magnesium sulfate and 468 parts of water are made into brine.
[0041] (4) 600.75 parts of magnesium oxide and 160.28 parts of dried bamboo scraps were added to brine and stirred evenly to obtain slurry A.
[0042] (5) Add 1.9 parts of the modified natural rubber latex into slurry A and stir rapidly at a rotational speed of 900 r / min for 300 seconds to obtain slurry B.
[0043...
Embodiment 2
[0045] A preparation method of natural rubber emulsion modified bamboo scraps / magnesium oxychloride composite material of the present invention, the amount of raw materials added is in parts by mass, comprising the following steps:
[0046] (1) Screening 70-mesh bamboo scraps and drying to a moisture content of 10%.
[0047] (2) adding 0.2 part of sodium lauryl sulfate to 3.6 parts of natural rubber latex, stirring evenly, and leaving for 5 days to fully react to obtain a modified natural rubber latex.
[0048] (3) Under normal temperature and pressure, 240.35 parts of magnesium chloride, 300.78 parts of magnesium sulfate and 468 parts of water are made into brine.
[0049] (4) 600.75 parts of magnesium oxide and 160.28 parts of dried bamboo scraps were added to brine and stirred evenly to obtain slurry A.
[0050] (5) Add 3.8 parts of modified natural rubber latex into slurry A, stir evenly, stir rapidly, and stir for 300 seconds at a rotational speed of 900 r / min to obtain ...
Embodiment 3
[0053] A preparation method of natural rubber emulsion modified bamboo scraps / magnesium oxychloride composite material of the present invention, the amount of raw materials added is in parts by mass, comprising the following steps:
[0054] (1) Screening 70-mesh bamboo scraps and drying to a moisture content of 10%.
[0055] (2) Add 0.3 parts of sodium lauryl sulfate to 5.4 parts of natural rubber latex, stir evenly, and leave for 5 days to fully react to obtain a modified natural rubber latex.
[0056] (3) Under normal temperature and pressure, 240.35 parts of magnesium chloride, 300.78 parts of magnesium sulfate and 468 parts of water are made into brine.
[0057] (4) 600.75 parts of magnesium oxide and 160.28 parts of dried bamboo scraps were added to brine and stirred evenly to obtain slurry A.
[0058] (5) Add 5.7 parts of the modified natural rubber latex into slurry A and stir rapidly at a rotational speed of 900 r / min for 300 seconds to obtain slurry B.
[0059] (6) ...
PUM
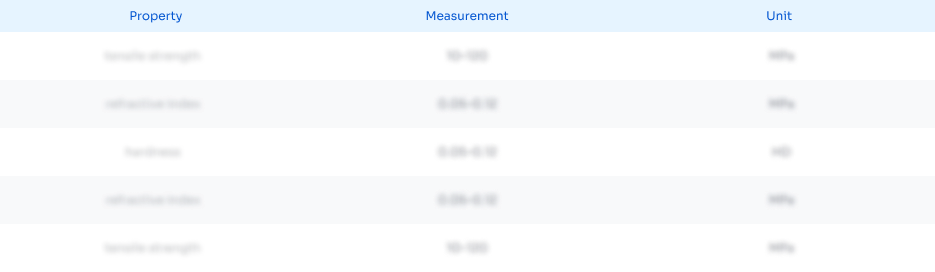
Abstract
Description
Claims
Application Information

- R&D Engineer
- R&D Manager
- IP Professional
- Industry Leading Data Capabilities
- Powerful AI technology
- Patent DNA Extraction
Browse by: Latest US Patents, China's latest patents, Technical Efficacy Thesaurus, Application Domain, Technology Topic, Popular Technical Reports.
© 2024 PatSnap. All rights reserved.Legal|Privacy policy|Modern Slavery Act Transparency Statement|Sitemap|About US| Contact US: help@patsnap.com