Method for forming thin-wall metal component by controlling inflation position
A metal component and thin-walled technology, which is applied in the field of forming thin-walled metal components by controlling the inflated position, can solve problems such as uneven distribution of wall thickness, weakening of component performance, cracking, etc., so as to solve the uneven distribution of wall thickness and improve the distribution of wall thickness Uniformity, the effect of simplifying the process flow
- Summary
- Abstract
- Description
- Claims
- Application Information
AI Technical Summary
Problems solved by technology
Method used
Image
Examples
Embodiment 1
[0028] Example 1: Combination figure 1 , figure 2 , Figure 3, Figure 4 illustrates, a method for controlling the inflation position to form a thin-walled metal member proposed by the present invention, the method is carried out according to the following steps:
[0029] Step 1. Determination of sheet forming scheme: Analyze the shape characteristics of thin-walled metal components, determine the material of the slab, use wire cutting to cut out the appropriate sheet size, and determine the sheet forming scheme through theoretical calculation or finite element simulation analysis.
[0030] Step 2. Design of the upper and lower air intake forming inserts: According to the characteristic size of the thin-walled metal components, design the corresponding characteristic contours of the upper and lower forming inserts, and analyze the thin-walled metal components that are prone to wall thickness reduction and thinning during the forming process. For the location of material accumu...
Embodiment 2
[0038] Embodiment 2: Referring to Fig. 3, in step 2, upper and lower air intake forming inserts of different shapes and sizes can be designed according to the forming needs. If a forming part with many local features is formed, it is necessary to design multiple shapes for the upper and lower inserts If the formed part has multiple large curvature features and the material flow behavior is complex, it is necessary to reasonably use finite element simulation software for calculation to analyze the material flow characteristics in the pre-forming and final forming process, and combine the calculation results for the upper air forming process. The pre-formed contour design is performed on the insert to make it pre-formed into a rough outline shape, and then the final forming contour design is performed on the lower air intake forming insert. The pre-forming and final forming effects are coupled to form an ideal forming with large curvature characteristics. It solves the problem th...
Embodiment 3
[0040] Embodiment 3: Referring to Fig. 3, in step 2, according to the shape characteristics of the thin-walled metal components, the corresponding air inlets are designed at different positions of the upper and lower air intake forming inserts. For example, when forming deep cavity thin-walled parts, the bottom If the wall thickness of the fillet area is thin, when designing the air inlet of the lower air intake forming insert, it is necessary to take into account the reasonable regulation of the material flow in the bottom fillet area during pre-forming, and use the flow characteristics of the material during inflation to reduce the thickness of the material in advance. Gather material in the area, that is, design the corresponding inflatable port at the corresponding position of the rounded area, gather the material during pre-forming, and then design the corresponding inflatable port on the upper air intake forming insert according to the wall thickness distribution character...
PUM
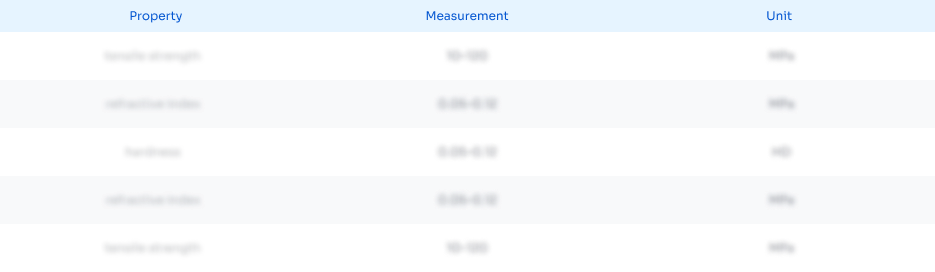
Abstract
Description
Claims
Application Information

- R&D Engineer
- R&D Manager
- IP Professional
- Industry Leading Data Capabilities
- Powerful AI technology
- Patent DNA Extraction
Browse by: Latest US Patents, China's latest patents, Technical Efficacy Thesaurus, Application Domain, Technology Topic, Popular Technical Reports.
© 2024 PatSnap. All rights reserved.Legal|Privacy policy|Modern Slavery Act Transparency Statement|Sitemap|About US| Contact US: help@patsnap.com