Modified epoxy resin and preparation method thereof
An epoxy resin preparation and epoxy resin technology, applied in the field of electric composite materials, can solve the problems of unfavorable performance uniformity, excessively long curing time, and long curing time, and achieve optimized processing and curing technology, simple processing technology conditions, and improved The effect of comprehensive mechanical properties
- Summary
- Abstract
- Description
- Claims
- Application Information
AI Technical Summary
Problems solved by technology
Method used
Image
Examples
Embodiment example 1
[0025] In a 500ml beaker, add 200g epoxy resin E44, 10g allyl glycidyl ether and 20g C12-C14 aliphatic glycidyl ether and mix evenly, then add 46g vinyl resin, stir and mix evenly to obtain the target modified polyepoxide Resin 1.
Embodiment example 2
[0027] In a 500ml beaker, add 200g epoxy resin E44, 10g allyl glycidyl ether and 20g C12-C14 aliphatic glycidyl ether and mix evenly, then add 69g vinyl resin, stir and mix evenly to obtain the target modified polyepoxy Resin 2.
Embodiment example 3
[0029] In a 500ml beaker, add 200g epoxy resin E44, 6g allyl glycidyl ether and 24g C12-C14 aliphatic glycidyl ether and mix evenly, then add 46g vinyl resin, stir and mix evenly to obtain the target modified polyepoxide Resin 3.
PUM
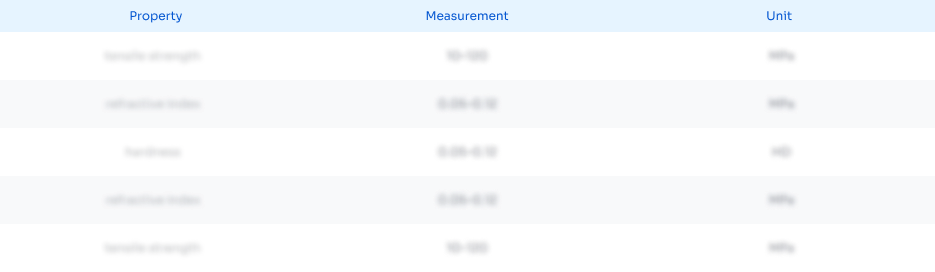
Abstract
Description
Claims
Application Information

- Generate Ideas
- Intellectual Property
- Life Sciences
- Materials
- Tech Scout
- Unparalleled Data Quality
- Higher Quality Content
- 60% Fewer Hallucinations
Browse by: Latest US Patents, China's latest patents, Technical Efficacy Thesaurus, Application Domain, Technology Topic, Popular Technical Reports.
© 2025 PatSnap. All rights reserved.Legal|Privacy policy|Modern Slavery Act Transparency Statement|Sitemap|About US| Contact US: help@patsnap.com