Chemical scale removing method for evaporator
An evaporator and chemical technology, which is applied in the field of chemical descaling of evaporators, can solve the problems of insufficient cleaning, time-consuming and labor-intensive, and scaling of three-effect evaporators, so as to avoid heat dissipation problems, reduce descaling time, and shorten cleaning time. The effect of the fouling cycle
- Summary
- Abstract
- Description
- Claims
- Application Information
AI Technical Summary
Problems solved by technology
Method used
Image
Examples
Embodiment 1
[0057] The evaporator cleaning process can be summarized as the following steps:
[0058] (1) prepare the sodium carbonate solution of 20wt% concentration in proportion in the dispensing tank, and heat the lye to 60 ℃ by steam; prepare the nitric acid solution of 10wt% concentration at normal temperature (25 ℃) in the acid dispensing tank;
[0059](2) The sodium carbonate solution is pumped into the first-effect, second-effect, and third-effect separators respectively through three feed pumps, and circulating cleaning is carried out separately in the three evaporation systems, and the cleaning temperature is controlled at 65 ° C, and the cleaning The sodium carbonate solution used during cleaning accounts for 55% of the volume of the cleaning container;
[0060] (3) After 30min of circulation, the sodium carbonate solution in the triple-effect evaporator is simultaneously discharged into the lye filter tank for filtration through the discharge pipe, and the filtrate is returne...
Embodiment 2
[0065] The evaporator cleaning process can be summarized as the following steps:
[0066] (1) the sodium carbonate solution of 15wt% concentration is prepared in proportion in the dispensing tank, and the lye is heated to 60 ℃ by steam; the nitric acid solution of 3wt% concentration is prepared at normal temperature (25 ℃) in the acid dispensing tank;
[0067] (2) The sodium carbonate solution is pumped into the first-effect, second-effect, and third-effect separators respectively through three feed pumps, and circulating cleaning is carried out separately in the three evaporation systems, and the cleaning temperature is controlled at 70 ° C, and the cleaning The sodium carbonate solution used during cleaning accounts for 60% of the volume of the cleaning container;
[0068] (3) After 30min of circulation, the sodium carbonate solution in the triple-effect evaporator is simultaneously discharged into the lye filter tank for filtration through the discharge pipe, and the filtra...
Embodiment 3
[0073] The evaporator cleaning process can be summarized as the following steps:
[0074] (1) prepare the sodium carbonate solution of 25wt% concentration in proportion in the dispensing tank, and heat the lye to 70 ℃ by steam; prepare the nitric acid solution of 6wt% concentration at normal temperature (25 ℃) in the acid dispensing tank;
[0075] (2) The sodium carbonate solution is pumped into the first-effect, second-effect, and third-effect separators respectively through three feed pumps, and circulating cleaning is carried out separately in the three evaporation systems, and the cleaning temperature is controlled at 75 ° C, and the cleaning The sodium carbonate solution used during cleaning accounts for 65% of the volume of the cleaning container;
[0076] (3) After 30min of circulation, the sodium carbonate solution in the triple-effect evaporator is simultaneously discharged into the lye filter tank for filtration through the discharge pipe, and the filtrate is returne...
PUM
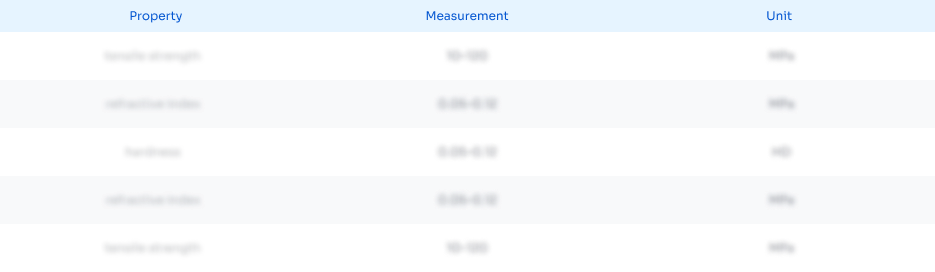
Abstract
Description
Claims
Application Information

- R&D
- Intellectual Property
- Life Sciences
- Materials
- Tech Scout
- Unparalleled Data Quality
- Higher Quality Content
- 60% Fewer Hallucinations
Browse by: Latest US Patents, China's latest patents, Technical Efficacy Thesaurus, Application Domain, Technology Topic, Popular Technical Reports.
© 2025 PatSnap. All rights reserved.Legal|Privacy policy|Modern Slavery Act Transparency Statement|Sitemap|About US| Contact US: help@patsnap.com