Manufacturing method of high-thermal-conductivity copper-clad ceramic substrate
A technology of copper-clad ceramic substrate and manufacturing method, which is applied in the direction of manufacturing tools, welding equipment, welding/welding/cutting items, etc., can solve the problems of high cost, environmental protection problems, poor tensile or shearing force performance, and achieve Reduce production cost, simple production process, and reliable connection
- Summary
- Abstract
- Description
- Claims
- Application Information
AI Technical Summary
Problems solved by technology
Method used
Image
Examples
specific Embodiment 1
[0027] Specific Example 1: Such as figure 1 As well as figure 2 As well as image 3 Show, a method of making a high -guide hot -covered copper ceramic substrate, which includes the following steps:
First, the copper sheet of the substrate is stamped and molded, which is made of a copper sheet 1A required by the high -guided thermal covering copper ceramic substrate;
[0028] Second, positioning the copper sheet and the substrate welding sheet to the substrate welding workpiece. Specifically, the substrate welded installation of the substrate includes the bottom plate 1. The upper pressure plate 3. The ceramic board limited tank on the surface of the bottom plate 1.1 and several settings are set on several settings. The copper sheet limited tank 1.2 on the bottom surface of the ceramic board 1.2. The bottom surface of the ceramic board limited tank between the two copper sheets restricted tanks is equipped with a pre -installed tank 2 on the bottom surface of the ceramic board, and...
PUM
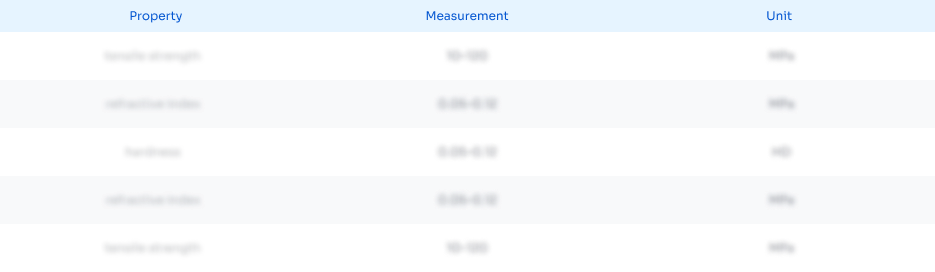
Abstract
Description
Claims
Application Information

- Generate Ideas
- Intellectual Property
- Life Sciences
- Materials
- Tech Scout
- Unparalleled Data Quality
- Higher Quality Content
- 60% Fewer Hallucinations
Browse by: Latest US Patents, China's latest patents, Technical Efficacy Thesaurus, Application Domain, Technology Topic, Popular Technical Reports.
© 2025 PatSnap. All rights reserved.Legal|Privacy policy|Modern Slavery Act Transparency Statement|Sitemap|About US| Contact US: help@patsnap.com