Processing equipment for composite fiber material capable of enhancing density
A composite fiber and processing equipment technology, applied in the cutting of textile materials, mechanical cleaning, textiles and papermaking, etc., can solve the problems of reducing the density of graphite felt, unable to drive graphite, polluting the environment, etc., and achieve the effect of increasing the density
- Summary
- Abstract
- Description
- Claims
- Application Information
AI Technical Summary
Problems solved by technology
Method used
Image
Examples
Embodiment 1
[0040] A processing equipment for composite fiber materials that can increase density, such as Figure 1-14 As shown, it includes a chassis 1, a conveying system 2, a needle punching system 3, a stretching system 4 and a fiber removal system 5; the left part of the upper surface of the chassis 1 and the right part of the upper surface are connected with the conveying system 2; The middle part of the surface is connected with an acupuncture system 3; the acupuncture system 3 is connected with a stretching system 4; the acupuncture system 3 is connected with a fiber removal system 5;
[0041] When in use, first place the processing equipment for the composite fiber material that can enhance the density at the required position, and place the bottom frame 1 on a stable position. First, the operator places a roll of graphite felt on the right side of the conveying system 2, Then pull the graphite felt out, pass through the acupuncture system 3, the stretching system 4 and the fibe...
Embodiment 2
[0043] On the basis of Example 1, such as Figure 1-14 As shown, the conveying system 2 includes a first conveying frame 201, a second conveying frame 202, a third conveying frame 203 and a fourth conveying frame 204; 1 The right part of the upper surface is fixedly connected with the second conveying frame 202, and the second conveying frame 202 is located on the left side of the first conveying frame 201; A fourth transport frame 204 is fixedly connected to the left part, and the fourth transport frame 204 is located on the left of the third transport frame 203 .
[0044] The acupuncture system 3 includes a fifth support frame 301, a first mounting bracket 302, a first motor 303, a first transmission roller 304, a first transmission wheel 305, a second transmission roller 306, a second transmission wheel 307, a third transmission Roller 308, sixth support frame 309, second mounting bracket 310, second motor 311, fourth transmission roller 312, third transmission wheel 313, ...
Embodiment 3
[0059] On the basis of Example 2, such as Figure 15 As shown, a cutting system 6 is also included; the left part of the upper surface of the bottom frame 1 is connected with a cutting system 6; the cutting system 6 includes a fifth conveying frame 601, a circular cutter 602 and a third collection box 603; The fifth conveyor frame 601 is fixedly connected to the left part of the surface, and the fifth conveyor frame 601 is located between the third conveyor frame 203 and the fourth conveyor frame 204; the front part and the rear part of the fifth conveyor frame 601 are respectively fixed with a conveyor roller. Circular cutter 602 ; two third collection boxes 603 are affixed to the upper left part of the bottom frame 1 , and the two third collection boxes 603 are located on the left of the fifth conveying frame 601 .
[0060] When the graphite felt slowly moves to the left, the conveying roller of the fifth conveying frame 601 is controlled to rotate, and the conveying roller ...
PUM
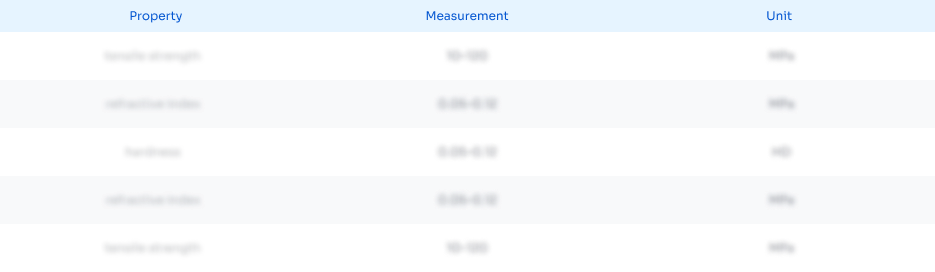
Abstract
Description
Claims
Application Information

- R&D
- Intellectual Property
- Life Sciences
- Materials
- Tech Scout
- Unparalleled Data Quality
- Higher Quality Content
- 60% Fewer Hallucinations
Browse by: Latest US Patents, China's latest patents, Technical Efficacy Thesaurus, Application Domain, Technology Topic, Popular Technical Reports.
© 2025 PatSnap. All rights reserved.Legal|Privacy policy|Modern Slavery Act Transparency Statement|Sitemap|About US| Contact US: help@patsnap.com