Polyethylene fiber concrete production device and preparation method thereof
A technology of polyethylene fiber and production equipment, applied in the field of squeeze casting, can solve the problems of inconvenient ratio of raw materials, affecting the quality of concrete, clumping and coagulation of cement, etc., and achieve the effect of improving the mixing effect
- Summary
- Abstract
- Description
- Claims
- Application Information
AI Technical Summary
Problems solved by technology
Method used
Image
Examples
Embodiment approach
[0054] In order to further better explain the above examples, the present invention also provides an embodiment, a preparation method of a polyethylene fiber concrete production device, comprising the following steps:
[0055] Step 1: First, sand and gravel and polypropylene fibers accounting for 1% of the total weight are pre-stored inside the tank body 11, then the drive motor 12 is started, and cement is loaded into the lower material box 314, and the cement passes through the second stage under the action of gravity. A feed port 315 and a second feed port 316 enter the inside of the feed box 312, and the drive motor 12 lifts the feed box 312 upwards through the material lifting assembly 32. When the discharge chute 313 and the feed chute 318 overlap, the cement Enter the inside of the tank body 11 through the discharge groove 313 and the feed groove 318, and when the feed box 312 moves upwards, the baffle plate 317 blocks the second feed port 316;
[0056] Step 2: Under th...
PUM
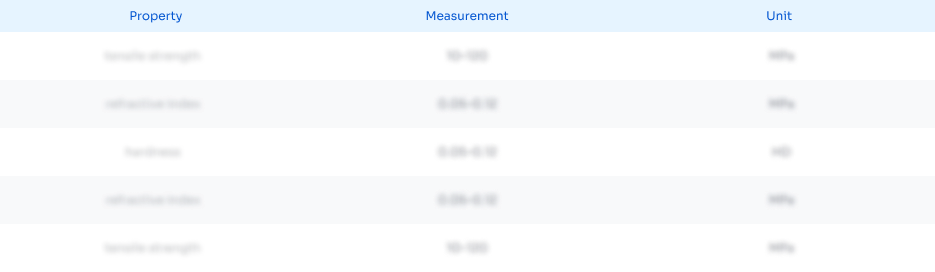
Abstract
Description
Claims
Application Information

- Generate Ideas
- Intellectual Property
- Life Sciences
- Materials
- Tech Scout
- Unparalleled Data Quality
- Higher Quality Content
- 60% Fewer Hallucinations
Browse by: Latest US Patents, China's latest patents, Technical Efficacy Thesaurus, Application Domain, Technology Topic, Popular Technical Reports.
© 2025 PatSnap. All rights reserved.Legal|Privacy policy|Modern Slavery Act Transparency Statement|Sitemap|About US| Contact US: help@patsnap.com