Production method of sugar cane sulfur-free white granulated sugar
A production method and technology of white granulated sugar, which is applied in sucrose production, sugar production, sugar juice purification, etc., can solve the problems of difficult environmental pollution, unsatisfactory clarification and decolorization effects, and high color value of products that are difficult to meet the standards. Reduce the degree of conversion and Maillard reaction, clarify the decolorization effect, improve the stability and shelf life
- Summary
- Abstract
- Description
- Claims
- Application Information
AI Technical Summary
Problems solved by technology
Method used
Image
Examples
Embodiment 1
[0030] A production method of sugarcane sulfur-free white sugar, comprising the following steps:
[0031] Step 1. Press the cane juice pre-ash: the use of the prior art for sugarcane pressing and extraction to obtain the mixed juice, the mixed juice into the mixed juice box to add 22 ° Belime milk for pre-ash, the end of the pre-ash pH value of 6.8, to obtain the pre-ash juice. In the process of white sugar production, after the sugarcane is directly pressed to obtain the primary pressure juice, it is necessary to add dilute cane juice or osmotic water to the bagasse, and the sucrose in the bagasse is extracted as much as possible through repeated pressing, and the cane juice extracted many times is mixed together to obtain mixed cane juice, the industry is referred to as mixed juice.
[0032] Step 2. Main ash: The pre-ash juice is heated to 43-45 °C, and then pumped into the high tank of the mixed juice, and the 22 °Be lime milk is added to the pre-ash juice according to the rati...
Embodiment 2
[0041] A production method of sugarcane sulfur-free white sugar, comprising the following steps:
[0042] Step 1. Press the cane juice pre-ash: The mixed juice obtained by the sugarcane squeezing and extraction is sent into the mixing tank and 18 °Bel lime milk is added to the pre-ash to obtain the pre-ash juice, and the pH of the pre-ash end is 7.1.
[0043] Step 2. Main ash: The pre-ash juice is heated to 41-43 °C, and then pumped into the mixed juice high trough, and the 18 °Be lime milk is added to the pre-ash juice according to the ratio of 1.6mg / L cane juice, so that the pH of the pre-ash juice is gradually increased to 10.5-11.0 to obtain the main ash juice.
[0044] Step 3: One carbon filling: The main ash juice is sent into a carbon filling tank, according to 1050m 3 / h flow through 95% purity co 2 For satiety, the one-carbon satiety process continues to add lime milk, according to the process requirements of the full juice pH 9.3-9.7, manually adjust the flow of lime mil...
Embodiment 3
[0052] A production method of sugarcane sulfur-free white sugar, comprising the following steps:
[0053] Step 1. Press the cane juice pre-ash: the mixed cane juice obtained by the sugarcane squeezing and extraction is sent to the mixing tank with 24 ° Bel lime milk for pre-ashing to obtain the pre-ash juice, and the pH of the end of the pre-ash is 7.2.
[0054] Step 2. Main ash: The pre-ash juice is heated to 40-42 °C, and then pumped into the mixed juice high trough, and the 24 °Be lime milk is added to the pre-ash juice according to the ratio of 2.0mg / L cane juice, so that the pH of the pre-ash juice is gradually increased to 10.5-11.0 to obtain the main ash juice.
[0055] Step 3. One carbon fullness: The main ash juice is filled with one carbon, according to 500m 3 / h flow through 95% purity co 2 For satiety, the one-carbon satiety process continues to add lime milk, and the pH automatic control system is used to control the amount of lime milk added to maintain the pH in the...
PUM
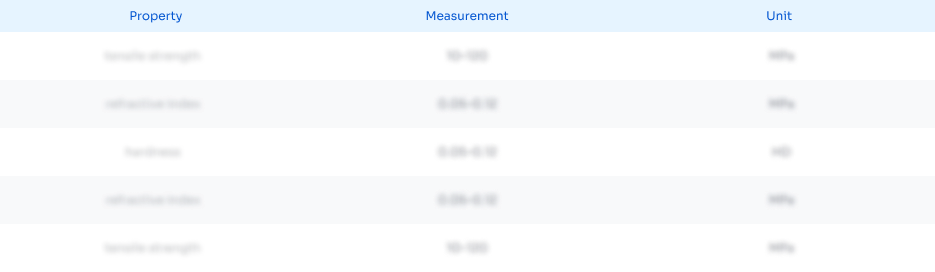
Abstract
Description
Claims
Application Information

- R&D
- Intellectual Property
- Life Sciences
- Materials
- Tech Scout
- Unparalleled Data Quality
- Higher Quality Content
- 60% Fewer Hallucinations
Browse by: Latest US Patents, China's latest patents, Technical Efficacy Thesaurus, Application Domain, Technology Topic, Popular Technical Reports.
© 2025 PatSnap. All rights reserved.Legal|Privacy policy|Modern Slavery Act Transparency Statement|Sitemap|About US| Contact US: help@patsnap.com