Methyl chlorosilane monomer separation and heat integration process design method
A technology of methylchlorosilane and heat integration, which is applied in chemical instruments and methods, organic chemistry, compounds of group 4/14 elements of the periodic table, etc., can solve problems such as difficult to break through energy consumption bottlenecks, and achieve cost reduction and reduction Effects of energy consumption and high energy efficiency
- Summary
- Abstract
- Description
- Claims
- Application Information
AI Technical Summary
Problems solved by technology
Method used
Image
Examples
Embodiment 1
[0017] Methylchlorosilane monomer distillation processes, such as Figure 1 as shown. The pre-sub-tower is divided into discontinuous key components by first and recombination, to achieve a clear separation of the two, 18% of the mass flow of the incoming material dia is distributed at the bottom of the tower, the heat load at the bottom of the tower accounts for 17% of the heating demand of the whole device, the theoretical number of plates and the feed position are designed as 200 and 20, the operating pressure range is 110-170kPa, the operating temperature range is 71.5-89.0 °C, and the return ratio is controlled at 1.1. The erjia tower takes the first and second A as the continuous key components, and the heat load at the bottom of the tower can account for 76%, the theoretical plate number and feed position are designed as 333 and 90, the operating pressure range is 110-211kPa, the operating temperature range is 61.8-95.3 °C, and the reflux ratio is controlled at 54.6. The ...
Embodiment 2
[0019] Methylchlorosilane monomer separation without dismantling columns for thermally integrated distillation processes, e.g Figure 2as shown. The theoretical number of plates and feed position of the pre-sub-tower are designed to be 171 and 12, respectively, the operating pressure range is 320-370kPa, the operating temperature range is 108.9-118.6 °C, and the return ratio is controlled at 3.1. The theoretical plate number and feed position of the erjia tower are designed to be 320 and 90, respectively, the operating pressure range is 110-210kPa, the operating temperature range is 61.8-94.6 °C, and the return ratio is controlled at 56.4. The theoretical plate number and feed position of the first tower are designed to be 111 and 55, respectively, the operating pressure range is 610-640kPa, the operating temperature range is 115.7-139.7 °C, and the return ratio is controlled at 5.9. The theoretical plate number and feed position of the removal tower are designed as 51 and 38, re...
Embodiment 3
[0021] Methylchlorosilane monomer separation feed combined with heavy-end segmentation thermal integrated distillation processes, e.g Figure 3as shown. The theoretical number of plates and feed position of the pre-sub-tower are designed to be 223 and 23, respectively, the operating pressure range is 300-370kPa, the operating temperature range is 106.9-118.6 °C, and the reflux ratio is controlled at 2.3. 59% of the distillate at the top of the pre-division tower enters the erjia A tower, and the rest enters the lower position of the erjia B tower. The theoretical plate number and feed position of the dijia A tower are designed to be 247 and 21, respectively, the operating pressure range is 320-400kPa, the operating temperature range is 108.5-120.4 °C, and the return ratio is controlled at 12.7. The theoretical plate number and feed position of Tower B are designed to be 285, 64 and 94, respectively, the operating pressure range is 110-200kPa, the operating temperature range is 61....
PUM
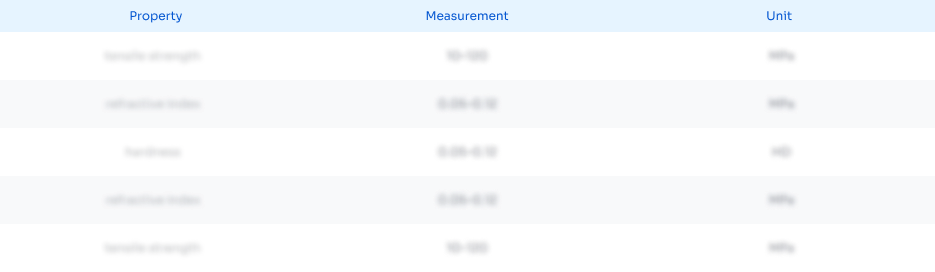
Abstract
Description
Claims
Application Information

- R&D
- Intellectual Property
- Life Sciences
- Materials
- Tech Scout
- Unparalleled Data Quality
- Higher Quality Content
- 60% Fewer Hallucinations
Browse by: Latest US Patents, China's latest patents, Technical Efficacy Thesaurus, Application Domain, Technology Topic, Popular Technical Reports.
© 2025 PatSnap. All rights reserved.Legal|Privacy policy|Modern Slavery Act Transparency Statement|Sitemap|About US| Contact US: help@patsnap.com