Method for selectively precipitating magnesium in zinc-magnesium solution
A magnesium solution and selective technology, applied in the field of hydrometallurgy, can solve the problems of lack of magnesium, residual extractant, increased production cost of zinc hydrometallurgy, etc.
- Summary
- Abstract
- Description
- Claims
- Application Information
AI Technical Summary
Problems solved by technology
Method used
Image
Examples
Embodiment 1
[0053] A method for removing magnesium in a hydrometallurgy process, wherein, comprising the following steps:
[0054] step one:
[0055] To the zinc sulfate solution (Zn 2+ : 60g / L, Mg 2+ : 40g / L), add formula 1-A, stir to dissolve; The addition of formula 1-A is 1.09 times of the molar weight of zinc in the solution; Pre-reaction 0.5h;
[0056] step two
[0057] Combined leaching agent solution (sodium carbonate and sodium hydroxide aqueous solution, wherein, the mol ratio of sodium carbonate and sodium hydroxide is 0.5:1; the concentration of sodium carbonate is 0.5M) and the pre-reaction solution of step 1 are pumped respectively with peristaltic pump Send it into a liquid flow (the flow rate of the liquid flow is, for example, 5-10mL / min), mix the two liquid flows, and collect the mixed solution in a container with a stirring structure, adjust the pumping flow rate of the solution, so that the mixing process The pH is maintained at 10-10.5; after the pumping of the pr...
Embodiment 2
[0064] A method for removing magnesium in a hydrometallurgy process, wherein, comprising the following steps:
[0065] step one:
[0066] To the zinc sulfate solution (Zn 2+ : 130g / L, Mg 2+ : 25g / L), add formula 1-A, stir until dissolved; the addition of formula 1-A is 0.8 times of the molar weight of zinc; pre-reaction 0.5h.
[0067] step two
[0068] Use a peristaltic pump to pump the combined leaching agent solution (aqueous solution of sodium bicarbonate and sodium hydroxide, the molar ratio of the two is 0.2:1, and the concentration of sodium bicarbonate is 0.2M) and the pre-reaction solution of step 1 into liquid respectively flow (the flow rate of the liquid flow is, for example, 5-10mL / min), the two liquid flows are mixed, and the mixed solution is collected in a container with a stirring structure, and the pumping flow rate of the solution is adjusted so that the pH during the mixing process is maintained at 10.5 ~ 11.0; after the pumping of the pretreatment liqui...
Embodiment 3
[0075] A method for removing magnesium in a hydrometallurgy process, wherein, comprising the following steps:
[0076] step one:
[0077] To the zinc sulfate solution (Zn 2+ : 100g / L, Mg 2+ : 60g / L), add formula 1-A, stir until dissolved; the addition of formula 1-A is 1.2 times the molar weight of zinc; pre-reaction 1h.
[0078] step two
[0079] Combined leaching agent solution (sodium carbonate and sodium hydroxide aqueous solution, wherein, the mol ratio of sodium carbonate and sodium hydroxide is 1:1; the concentration of sodium carbonate is 1M) and the pre-reaction liquid of step 1 are pumped respectively with peristaltic pump into a liquid flow (the flow rate of the liquid flow is, for example, 5-10mL / min), mix the two liquid flows, and collect the mixed solution in a container with a stirring structure, adjust the pumping flow rate of the solution, and make the pH during the mixing process Maintain at 10-10.5; after the pumping of the pretreatment solution is compl...
PUM
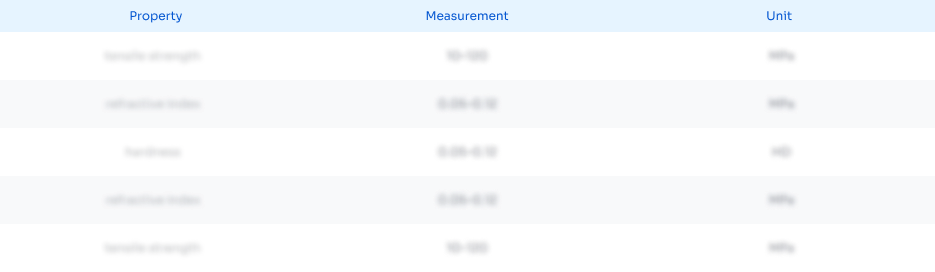
Abstract
Description
Claims
Application Information

- R&D
- Intellectual Property
- Life Sciences
- Materials
- Tech Scout
- Unparalleled Data Quality
- Higher Quality Content
- 60% Fewer Hallucinations
Browse by: Latest US Patents, China's latest patents, Technical Efficacy Thesaurus, Application Domain, Technology Topic, Popular Technical Reports.
© 2025 PatSnap. All rights reserved.Legal|Privacy policy|Modern Slavery Act Transparency Statement|Sitemap|About US| Contact US: help@patsnap.com