Raw material melting and mixing device for packaging plastic production and implementation method of raw material melting and mixing device
A technology for packaging and plastics, applied in the field of plastics production, can solve problems such as inability to unload raw materials, uneven fusion, waste materials, etc., and achieve the effects of improving recycling efficiency, avoiding energy waste, and improving uniformity
- Summary
- Abstract
- Description
- Claims
- Application Information
AI Technical Summary
Problems solved by technology
Method used
Image
Examples
Embodiment approach
[0042] In order to better demonstrate the implementation process of the packaging plastic production raw material blending device, this embodiment proposes an implementation method of the packaging plastic production raw material blending device, including the following steps:
[0043] Step 1: the plastic production raw material is fed into the mixing tank 2 through the feed pipe 21, the heating ring 41 heats the plastic production raw material in the mixing tank 2, and the temperature detector 44 controls the temperature of the heating ring 41;
[0044] Step 2: During the heating process, the stirring motor 51 drives the rotating rod 52 to rotate, and the rotating rod 52 drives the stirring rod 55 to rotate. When the stirring rod 55 is stirring, the internal heating rod 551 heats the raw materials for plastic production to effectively mix the raw materials;
[0045] Step 3: The scraper motor 61 drives the screw rod 62 to rotate. When rotating, the moving ring seat 64 is driven...
PUM
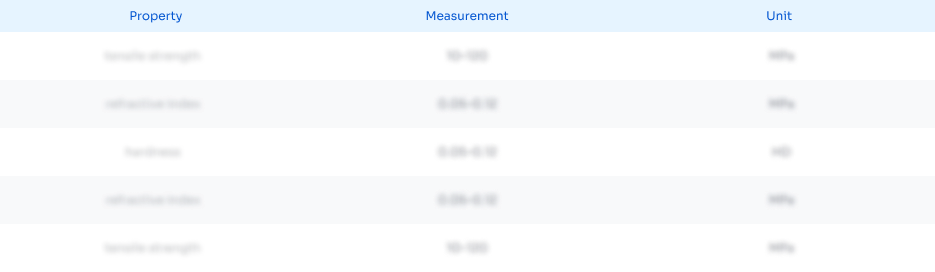
Abstract
Description
Claims
Application Information

- R&D Engineer
- R&D Manager
- IP Professional
- Industry Leading Data Capabilities
- Powerful AI technology
- Patent DNA Extraction
Browse by: Latest US Patents, China's latest patents, Technical Efficacy Thesaurus, Application Domain, Technology Topic, Popular Technical Reports.
© 2024 PatSnap. All rights reserved.Legal|Privacy policy|Modern Slavery Act Transparency Statement|Sitemap|About US| Contact US: help@patsnap.com