Tapered cutout configuration
A tapered, fin-shaped technology, applied in the field of improvement of drywall panels or panels, which can solve problems such as unfavorable sound-absorbing function, loss of function of sound-absorbing holes, etc.
- Summary
- Abstract
- Description
- Claims
- Application Information
AI Technical Summary
Problems solved by technology
Method used
Image
Examples
Embodiment Construction
[0016] figure 1 The non-tapered end of the drywall panel 10 is shown. As is conventional, the board 10 is manufactured with rectangular faces and has a gypsum core 11 encased in and bonded to a face paper layer 12 and a back paper layer 13 . The long sides of the rectangular plate 10 are tapered, as is customary in the industry. Manufactured or factory long side taper is achieved by reducing the thickness of the gypsum continuum at the edges of the core 11 . Typically, the board or panel 10 has major dimensions of 4 feet by 8 feet, 10 feet or 12 feet. In the example shown, the panel 10 is nominally 5 / 8 inch thick and has an acoustic construction as disclosed in US Pat. Nos. 8,684,134, 8,770,345 and 8,925,677. The board 10, including the paper wraps 12, 13, is perforated with circular holes, eg, 0.312 inches (8 mm) in diameter, with a total open area of between about 12% and 20%. The perimeter of the panel 10, for example a 5-1 / 2 inch wide area, is not perforated. The fr...
PUM
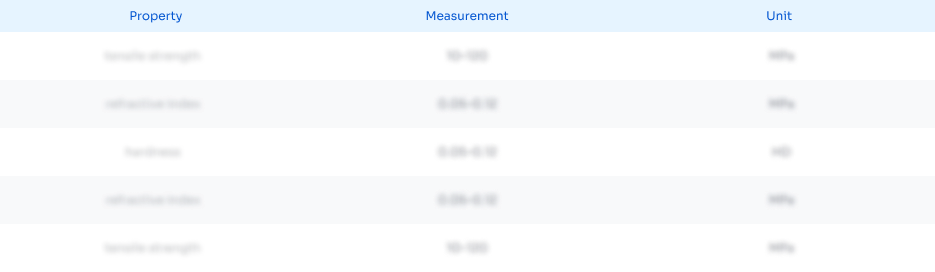
Abstract
Description
Claims
Application Information

- R&D Engineer
- R&D Manager
- IP Professional
- Industry Leading Data Capabilities
- Powerful AI technology
- Patent DNA Extraction
Browse by: Latest US Patents, China's latest patents, Technical Efficacy Thesaurus, Application Domain, Technology Topic, Popular Technical Reports.
© 2024 PatSnap. All rights reserved.Legal|Privacy policy|Modern Slavery Act Transparency Statement|Sitemap|About US| Contact US: help@patsnap.com