Water turbine volute internal corner backfill grouting auxiliary structure and backfill grouting method
A backfill grouting and auxiliary structure technology, which is applied in filling, infrastructure engineering, hydropower generation, etc., can solve the problems of arranging grouting boxes and grouting pipes, poor grouting effect, and long grouting pipes, etc. Easy grouting and low grouting pressure
- Summary
- Abstract
- Description
- Claims
- Application Information
AI Technical Summary
Problems solved by technology
Method used
Image
Examples
Embodiment Construction
[0025] The present invention will be further described below in conjunction with the accompanying drawings and specific embodiments.
[0026] Such as figure 1 As shown, an auxiliary structure for backfilling and grouting of the inner corner of the volute of a water turbine according to the present invention is used for backfilling and grouting the inner corner of the volute 6 between the inner side of the volute 2 and the seat ring 1, and is characterized in that it includes a temporary The support seat 3, the inner formwork 4 and the grouting pipe 5, a number of temporary support seats 3 and the inner formwork 4 are arranged around the bottom of the seat ring 1, the inner formwork 4 is vertically arranged on the inner side of the temporary support seat 3, and the grouting pipe 5 extends from the inner side of the seat ring 1 through the gap between the inner template 4 and the adjacent temporary support seat 3 to the inner corner part 6 of the volute.
[0027] The inlet end ...
PUM
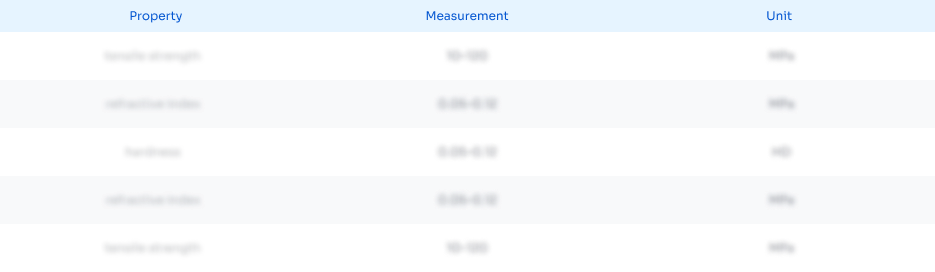
Abstract
Description
Claims
Application Information

- R&D
- Intellectual Property
- Life Sciences
- Materials
- Tech Scout
- Unparalleled Data Quality
- Higher Quality Content
- 60% Fewer Hallucinations
Browse by: Latest US Patents, China's latest patents, Technical Efficacy Thesaurus, Application Domain, Technology Topic, Popular Technical Reports.
© 2025 PatSnap. All rights reserved.Legal|Privacy policy|Modern Slavery Act Transparency Statement|Sitemap|About US| Contact US: help@patsnap.com