Numerical control rotary table
A technology of rotary workbench and tabletop, which is applied in the direction of manufacturing tools, metal processing equipment, metal processing machinery parts, etc. It can solve the problems of large deformation of the workbench under pressure, difficulty in meeting precision machining, difficulty in guaranteeing service life, etc., and achieve stable operation High performance, guaranteed machining accuracy, and good axial accuracy
- Summary
- Abstract
- Description
- Claims
- Application Information
AI Technical Summary
Problems solved by technology
Method used
Image
Examples
Embodiment approach
[0046] Such as Figure 1 to Figure 5 As shown, the present invention also has a second embodiment. The structure of this embodiment is basically similar to that of the first embodiment, and the difference lies in the addition of a sub-table 5 .
[0047] In this embodiment, a sub-table 5 is fixedly installed on the top of the table 1 .
[0048] The design of the sub-table 5 is mainly due to the load bearing considerations for large-sized workpieces. For large-sized workpieces, the smaller table top 1 is difficult to fix the workpiece stably, and the workpiece is easy to shake or shake during operation. After the auxiliary table 5 is used, the auxiliary table 5 can be designed according to the size of the workpiece to meet the needs of fixing.
[0049] Instead of directly adopting a large-sized table top 1, it is entirely out of consideration of stable operation and bearing capacity. With a large-sized table top 1, the bearing capacity distribution is too complicated, and it i...
experiment example
[0056] The force analysis is carried out on the rotary table designed in the first embodiment of the present invention to detect whether the design of the present invention can meet the bearing requirements.
[0057] Apply a force of 400,000N (40t) within the range of diameter 2293mm to 3800mm on the table surface, and conduct finite element simulation analysis on the strength of the table. The analysis results are shown in Figure 7 .
[0058] Depend on Figure 7 It can be seen from the displayed analysis results that the maximum deformation of the table 1 of the rotary table of the present invention occurs at the outermost edge of the table 1, and the maximum deformation is 0.027mm, which is extremely small and belongs to elastic deformation, and its influence on welding and the use of the turntable can be ignored .
[0059] It can be seen from the results of the experimental example that the present invention can meet the requirement of high-precision load bearing of 40 t...
PUM
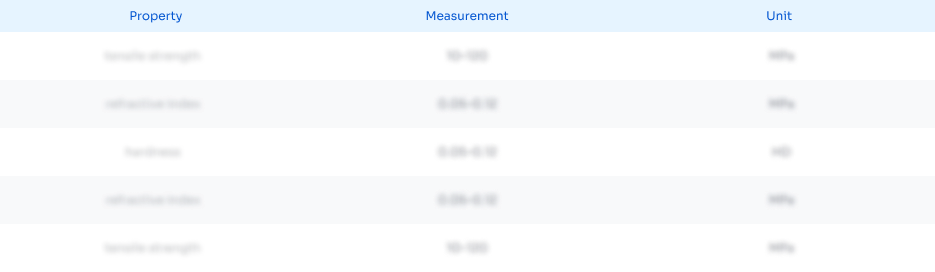
Abstract
Description
Claims
Application Information

- Generate Ideas
- Intellectual Property
- Life Sciences
- Materials
- Tech Scout
- Unparalleled Data Quality
- Higher Quality Content
- 60% Fewer Hallucinations
Browse by: Latest US Patents, China's latest patents, Technical Efficacy Thesaurus, Application Domain, Technology Topic, Popular Technical Reports.
© 2025 PatSnap. All rights reserved.Legal|Privacy policy|Modern Slavery Act Transparency Statement|Sitemap|About US| Contact US: help@patsnap.com