Numerical control machine tool multi-working-condition cutting parameter optimization method based on multilayer perceptron
A multi-layer perceptron and CNC machine tool technology, applied in the direction of digital control, program control, electrical program control, etc., can solve the problems of offset and influence between processing parts and machine tool tools, and unfavorable quality and performance of processed workpieces. Achieve the effect of improving efficiency and good data fitting effect
- Summary
- Abstract
- Description
- Claims
- Application Information
AI Technical Summary
Problems solved by technology
Method used
Image
Examples
Embodiment Construction
[0040] The technical solutions in the embodiments of the present invention will be described clearly and in detail below with reference to the drawings in the embodiments of the present invention. The described embodiments are only some of the embodiments of the invention. The technical scheme that the present invention solves the problems of the technologies described above is:
[0041] The overall process of the research method for the optimization of cutting machining parameters under multiple working conditions under the uncertainty of spindle coordinates and tool parameters in CNC machine tool milling is as follows: figure 1 As shown, the present invention takes a vertical machining center as an example for analysis. First, the orthogonal experiment is used to design the discrete machine tool workspace, tool diameter, and overhang length, and then combined with the hammering modal experiment method, the workpiece-tool system is obtained. The frequency response function c...
PUM
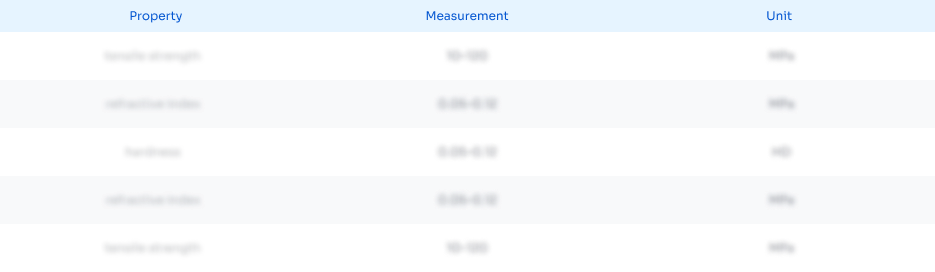
Abstract
Description
Claims
Application Information

- R&D
- Intellectual Property
- Life Sciences
- Materials
- Tech Scout
- Unparalleled Data Quality
- Higher Quality Content
- 60% Fewer Hallucinations
Browse by: Latest US Patents, China's latest patents, Technical Efficacy Thesaurus, Application Domain, Technology Topic, Popular Technical Reports.
© 2025 PatSnap. All rights reserved.Legal|Privacy policy|Modern Slavery Act Transparency Statement|Sitemap|About US| Contact US: help@patsnap.com