Preparation method of iron-containing zirconium alloy cast ingot
A zirconium alloy and ingot casting technology, which is applied in the field of preparation of iron-containing zirconium alloy ingots, can solve the problems of poor uniformity and increasing control difficulty, and achieve the effects of uniform distribution, stable product quality and good performance
- Summary
- Abstract
- Description
- Claims
- Application Information
AI Technical Summary
Problems solved by technology
Method used
Image
Examples
preparation example Construction
[0032] A method for preparing an iron-containing zirconium alloy ingot, comprising the following steps:
[0033] Step 1. Select sponge zirconium and pure iron filings / granules, the weight of pure iron filings / granules accounts for 10% to 20% of the total weight, and the size of the iron filings is: length 3-8mm, width 2-5mm, thickness 0.1-0.2 mm, according to the required weight of each electrode block, divide the sponge zirconium and iron filings into several equal parts, and each equal part is used to press an electrode block: first divide each equal part of sponge zirconium into half and add it to the press In the mold cavity, sprinkle iron filings evenly on the sponge zirconium in the mold cavity, then add the other half of the sponge zirconium, and finally press it on a 50MN press, where the electrode block is a rod-shaped electrode;
[0034] Step 2. Weld a plurality of electrode blocks in a vacuum plasma welding box to form a consumable electrode. The welding current is ...
Embodiment 1
[0045] Step 1. Select sponge zirconium and prepared pure iron filings (brand YT-1), and calculate the required sponge zirconium and iron filings weights according to the Fe element content and feeding amount in sponge zirconium. In this embodiment, the weight of Fe accounts for the total The feeding ratio is 10%, the total feeding is 500kg, the size of iron filings: length×width×thickness: 3mm×2mm×0.2mm;
[0046] Step 2, preparing the prepared zirconium sponge and iron filings into electrodes; the electrode preparation process includes the following steps:
[0047] Electrode pressing: The weighed zirconium sponge and iron filings are jointly pressed into 20 electrode blocks with a weight of 25kg / block, and the specification is Φ110mm×300mm. When pressing, divide the weighed zirconium sponge into half and add it to the cavity of the press. Then add the weighed iron filings and sprinkle evenly on the sponge zirconium in the mold cavity, then add the other half of the sponge zirc...
Embodiment 2
[0060] Step 1. Select sponge zirconium and prepared pure iron filings (brand YT-1), and calculate the required sponge zirconium and iron filings weights according to the Fe element content and feeding amount in sponge zirconium. In this embodiment, the weight of Fe accounts for the total The feeding ratio is 15%, the total feeding is 660kg, the size of iron filings: length×width×thickness: 5mm×3mm×0.2mm;
[0061] Step 2, preparing the prepared zirconium sponge and iron filings into electrodes; the electrode preparation process includes the following steps:
[0062] Electrode pressing: The weighed zirconium sponge and iron filings are jointly pressed into 22 electrode blocks with a weight of 30kg / block, and the specification is Φ160mm×300mm. When pressing, divide the weighed zirconium sponge into half and add it to the cavity of the press. Then add the weighed iron filings and sprinkle evenly on the sponge zirconium in the mold cavity, then add the other half of the sponge zirc...
PUM
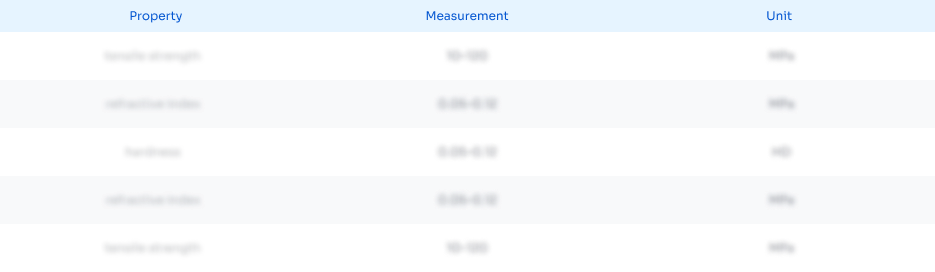
Abstract
Description
Claims
Application Information

- R&D Engineer
- R&D Manager
- IP Professional
- Industry Leading Data Capabilities
- Powerful AI technology
- Patent DNA Extraction
Browse by: Latest US Patents, China's latest patents, Technical Efficacy Thesaurus, Application Domain, Technology Topic, Popular Technical Reports.
© 2024 PatSnap. All rights reserved.Legal|Privacy policy|Modern Slavery Act Transparency Statement|Sitemap|About US| Contact US: help@patsnap.com