Method for controlling quality of water turbine guide vane casting through double-loop conductive crystallizer electroslag remelting
An electroslag remelting and crystallizing technology, which is applied in the directions of casting molds, casting mold components, manufacturing tools, etc., can solve the problems of difficult process design, high production cost, poor process stability, etc., and achieve good solidification quality and surface quality. , the effect of reducing production costs and reducing the amount of subsidies
- Summary
- Abstract
- Description
- Claims
- Application Information
AI Technical Summary
Problems solved by technology
Method used
Image
Examples
Embodiment 1
[0045] A method for controlling the quality of turbine guide vane castings by electroslag remelting in a double-circuit conductive crystallizer. The schematic diagram of electroslag remelting is as follows figure 1 As shown, the wiring position of the conductive upper crystallizer is at the upper end of the crystallizer, and the wiring copper plate is installed and fixed on the wiring board on the top of the conductive upper mold. Shaft conduction, reducing the conductive window of the electroslag remelting process, the material of the consumable electrode is ZG0Cr13Ni4Mo martensitic stainless steel, including the following steps:
[0046] Step 1), the baking of slag:
[0047] After baking a sufficient amount of slag material ANF-6 (30% Al2O3 + 70% CaF2) at 800°C for 4 hours, the slag material is cooled with the furnace and set aside;
[0048] Step 2), prepare materials:
[0049] (1) Determine the amount of slag and the filling ratio of the upper and lower crystallizers: the...
PUM
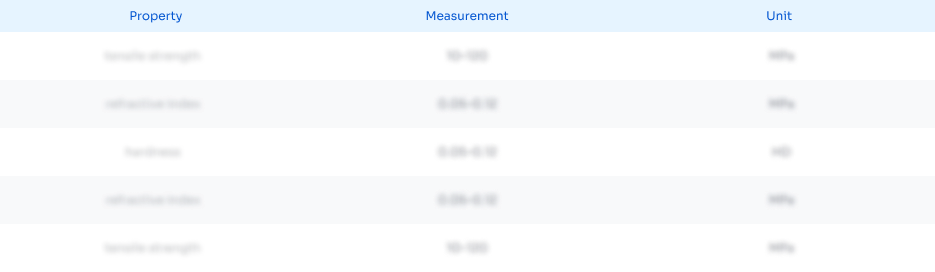
Abstract
Description
Claims
Application Information

- Generate Ideas
- Intellectual Property
- Life Sciences
- Materials
- Tech Scout
- Unparalleled Data Quality
- Higher Quality Content
- 60% Fewer Hallucinations
Browse by: Latest US Patents, China's latest patents, Technical Efficacy Thesaurus, Application Domain, Technology Topic, Popular Technical Reports.
© 2025 PatSnap. All rights reserved.Legal|Privacy policy|Modern Slavery Act Transparency Statement|Sitemap|About US| Contact US: help@patsnap.com