Production method of cooling fin for friction stir welding
A friction stir welding and production method technology, applied in welding equipment, welding equipment, non-electric welding equipment and other directions, can solve problems such as affecting product quality, damage to heat dissipation fins, etc., to achieve the effect of good quality
- Summary
- Abstract
- Description
- Claims
- Application Information
AI Technical Summary
Problems solved by technology
Method used
Image
Examples
Embodiment Construction
[0040] The present application will be further described in detail below with reference to the accompanying drawings.
[0041] The present application discloses a method of producing a heat sink for stirring friction, including the following steps:
[0042] Decreased, cutting the long raw material into a plurality of short films, the length of the long raw material is 5m, and the length of the automatic lowering machine is required to be cut, the length of the short material is 400 mm in this embodiment, when cutting The long raw material is pressed, and the length of the cutting needs to be cut, and the short film is cut by a cutter.
[0043] The calibration end surface is then performed, and the heat dissipating fin 12 is formed by the calibration clamp, and the substrate 11 is fixed by the clamp, so that the calibration clamp is relatively moved with the heat sink, and the heat dissipating fins 12 are calibrated to each other. The state is cut, and the heat dissipating fin 12 i...
PUM
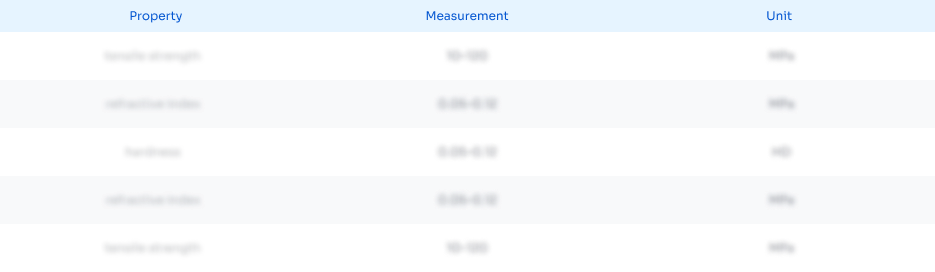
Abstract
Description
Claims
Application Information

- R&D
- Intellectual Property
- Life Sciences
- Materials
- Tech Scout
- Unparalleled Data Quality
- Higher Quality Content
- 60% Fewer Hallucinations
Browse by: Latest US Patents, China's latest patents, Technical Efficacy Thesaurus, Application Domain, Technology Topic, Popular Technical Reports.
© 2025 PatSnap. All rights reserved.Legal|Privacy policy|Modern Slavery Act Transparency Statement|Sitemap|About US| Contact US: help@patsnap.com