Trimming knife welding machine
A technology of trimming knife and welding machine, which is applied in welding equipment, high-frequency current welding equipment, metal processing equipment, etc., can solve the problems of limited controllable range of clamping device, complicated operation, and inability to guarantee welding quality and quality.
- Summary
- Abstract
- Description
- Claims
- Application Information
AI Technical Summary
Problems solved by technology
Method used
Image
Examples
Embodiment Construction
[0035] The present specific embodiment is merely an explanation of the present invention, which is not limited to the present invention, and those skilled in the < It is required to be protected by patent law.
[0036] See Figure 1-9 In this example, a trimming knife welding machine is disclosed, including a machine, and a first feed apparatus 3 for conveying the trimming knife workpiece and a shift for controlling the movement of the trimming tool. The material 2 is provided, and the other side is provided with a sheet device 4 for the trimming tool on the first feed apparatus 3 to the shifting device 2 and the cutting slide for flying the cutting edge into the trimming tool. The second feed device 5, the upper device 4 and the second feed apparatus 5 are provided with a welding station 12, and a welding device 6 is provided below, and the welding station is provided above. The mounting frame 11 is provided on the mounting frame 11, an angle detecting device 7, an upper rubber de...
PUM
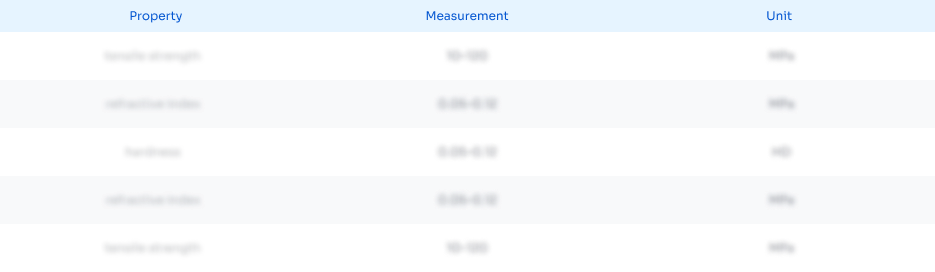
Abstract
Description
Claims
Application Information

- R&D
- Intellectual Property
- Life Sciences
- Materials
- Tech Scout
- Unparalleled Data Quality
- Higher Quality Content
- 60% Fewer Hallucinations
Browse by: Latest US Patents, China's latest patents, Technical Efficacy Thesaurus, Application Domain, Technology Topic, Popular Technical Reports.
© 2025 PatSnap. All rights reserved.Legal|Privacy policy|Modern Slavery Act Transparency Statement|Sitemap|About US| Contact US: help@patsnap.com