Formed grinding wheel gear grinding machine tool
A technology for forming grinding wheels and grinding teeth, which is applied to gear teeth, parts of grinding machine tools, mechanical equipment, etc., can solve the problems of affecting processing efficiency, low processing accuracy, and high proportion of auxiliary time, so as to improve meshing stability and improve The effect of processing efficiency and good process guarantee
- Summary
- Abstract
- Description
- Claims
- Application Information
AI Technical Summary
Problems solved by technology
Method used
Image
Examples
Embodiment Construction
[0038] In order to enable those skilled in the art to better understand the technical solutions of the present invention, the present invention will be further described in detail below in conjunction with the accompanying drawings and specific embodiments.
[0039] See figure 1 , which is a schematic diagram of a use state of the profile grinding wheel gear grinding machine tool described in this embodiment.
[0040] The form grinding wheel gear grinding machine tool includes five linear axes of X, Y, Z, W and W1 and seven rotary axes of A, B, B1, B2 and C under the use state of grinding external teeth. Here, "linear axis" refers to the motion displacement relationship between the matching components in the corresponding linear direction, and "rotational axis" means the motion displacement relationship between the matching components in the corresponding rotation direction. It should be understood that the above-mentioned dimension limitations are used to clearly describe t...
PUM
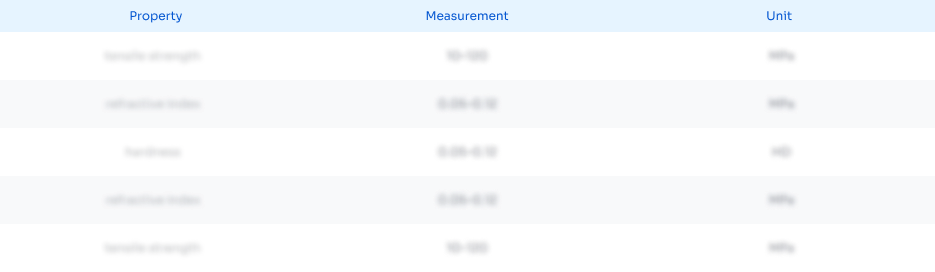
Abstract
Description
Claims
Application Information

- R&D
- Intellectual Property
- Life Sciences
- Materials
- Tech Scout
- Unparalleled Data Quality
- Higher Quality Content
- 60% Fewer Hallucinations
Browse by: Latest US Patents, China's latest patents, Technical Efficacy Thesaurus, Application Domain, Technology Topic, Popular Technical Reports.
© 2025 PatSnap. All rights reserved.Legal|Privacy policy|Modern Slavery Act Transparency Statement|Sitemap|About US| Contact US: help@patsnap.com