Preparation method of nano calcium carbonate
A technology of nano-calcium carbonate and calcium carbonate ore, which is applied in the fields of calcium carbonate/strontium/barium, chemical instruments and methods, calcium/strontium/barium compounds, etc., which can solve the problem that the product is harmful to the human body, cannot be applied in the field of food and medicine, and the steps are cumbersome, etc. question
- Summary
- Abstract
- Description
- Claims
- Application Information
AI Technical Summary
Problems solved by technology
Method used
Image
Examples
Embodiment 1
[0024] Step 1: put the crushed, ground and screened calcium carbonate raw material into a muffle furnace for calcination at 1000°C.
[0025] Step 2: Take 5.6g of calcined calcium oxide, dissolve it in 200ml of deionized water, pour it into a three-necked flask, digest it in a water bath at 70°C, stir vigorously at 1000rpm with a magnetic stirrer for 3 hours, and age it for 24 hours after digestion.
[0026] Step 3: Place the flask in a water bath at 25° C. and vigorously stir at 1000 rpm with a magnetic stirrer.
[0027] Step 4: Insert the catheter with the porous quartz stone connected to the head below the liquid surface, as close to the bottom as possible, and inject carbon dioxide at a ventilation rate of 50ml / min.
[0028] Step 5: when ventilating for 45min, the solution pH=7, continued excessive ventilating for 30min, and ventilating for 75min, at this moment, the solution pH=6.78, stopped ventilating, and the product was suction filtered, washed and dried to obtain calc...
Embodiment 2
[0030] Step 1: put the crushed, ground and screened calcium carbonate raw material into a muffle furnace for calcination at 1000°C.
[0031] Step 2: Take 5.6g of calcined calcium oxide, dissolve it in 200ml of deionized water, pour it into a three-necked flask, digest it in a water bath at 70°C, stir vigorously at 1000rpm with a magnetic stirrer for 3 hours, and age it for 24 hours after digestion.
[0032] Step 3: Take 0.304g of xylitol, put it into a three-necked flask, place the flask in a 25°C water bath, and stir vigorously at 1000rpm with a magnetic stirrer.
[0033] Step 4: Insert the catheter with the porous quartz stone connected to the head below the liquid surface on the right side, as close to the bottom as possible, and inject carbon dioxide at a ventilation rate of 50ml / min. Samples were taken every 15 min for morphology observation.
[0034] Step 5: After the solution pH=7, continue to ventilate for 30min, at this moment, the solution pH=6, stop ventilating, th...
PUM
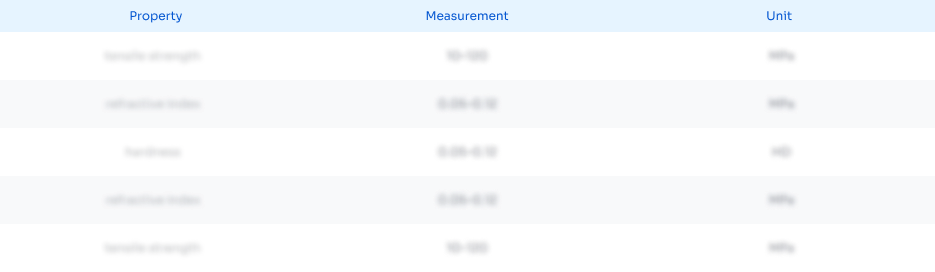
Abstract
Description
Claims
Application Information

- R&D Engineer
- R&D Manager
- IP Professional
- Industry Leading Data Capabilities
- Powerful AI technology
- Patent DNA Extraction
Browse by: Latest US Patents, China's latest patents, Technical Efficacy Thesaurus, Application Domain, Technology Topic, Popular Technical Reports.
© 2024 PatSnap. All rights reserved.Legal|Privacy policy|Modern Slavery Act Transparency Statement|Sitemap|About US| Contact US: help@patsnap.com