Ultrasonic nondestructive testing device for pipeline defects
A non-destructive testing and ultrasonic technology, applied in measuring devices, using sonic/ultrasonic/infrasonic waves to analyze solids, and using sonic/ultrasonic/infrasonic waves for material analysis, etc. Reduce consumption costs, overcome strong liquidity, and ensure the effect of accuracy
- Summary
- Abstract
- Description
- Claims
- Application Information
AI Technical Summary
Problems solved by technology
Method used
Image
Examples
Embodiment 1
[0028] An ultrasonic non-destructive testing device for pipeline defects, comprising a testing frame 1 and four Mecanum wheels 2 controlled by independent motors installed at the bottom of the testing frame 1, and an ultrasonic non-destructive testing box 3 is fixedly installed in the middle of the testing frame 1 , a number of reverse thrust fan blades 4 are fixedly installed on the side of the ultrasonic nondestructive testing box 3;
[0029] The ultrasonic non-destructive testing box 3 is equipped with a filter cabin 5 and a liquid supply cabin 6. The filter cabin 5 and the liquid supply cabin 6 are connected through a transition pipe 7. The pipe 9 communicates with the driven liquid supply pipe 11 through the flexible pipe 10, the liquid outlet of the driven liquid supply pipe 11 is located in the detection area 13 provided at the bottom of the detection probe 12, and the detection probe 12 is arranged in the ultrasonic nondestructive testing box 3 In the detection cabin 1...
Embodiment 2
[0032] In this embodiment, a water injection port 19 and a filter port 20 are respectively provided on one side of the ultrasonic non-destructive testing box 3 where the filter cabin 5 is located. The water port 19 replenishes water into the filter cabin 5, and the circulating impurities in the filter cabin 5 are cleaned through the filter port 20.
Embodiment 3
[0034] In this embodiment, a grid filter plate 22 is fixedly installed in the filter cabin 5, the water injection port 19 and the filter port 20 are respectively located on the upper and lower sides of the grid filter plate 22, and the transition pipe 7 is arranged in the filter cabin 5 near the water injection port 19. On one side, impurities are filtered through the grid filter plate 22, so as to ensure that the liquid entering the transition pipe 7 is kept clean, thereby ensuring the accuracy of flaw detection.
PUM
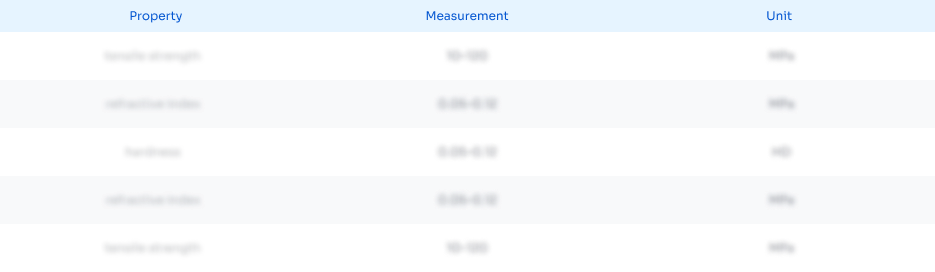
Abstract
Description
Claims
Application Information

- R&D
- Intellectual Property
- Life Sciences
- Materials
- Tech Scout
- Unparalleled Data Quality
- Higher Quality Content
- 60% Fewer Hallucinations
Browse by: Latest US Patents, China's latest patents, Technical Efficacy Thesaurus, Application Domain, Technology Topic, Popular Technical Reports.
© 2025 PatSnap. All rights reserved.Legal|Privacy policy|Modern Slavery Act Transparency Statement|Sitemap|About US| Contact US: help@patsnap.com