Silicon dioxide micropowder filler composition for high-thermal-conductivity and high-fluidity EMC (Electro Magnetic Compatibility) and preparation method thereof
A technology of silica and high fluidity, applied in chemical instruments and methods, heat exchange materials, etc., can solve the problems of high storage modulus, low filler content, low bending strength, etc., achieve high packaging integration, improve Filling, close-packed effect
- Summary
- Abstract
- Description
- Claims
- Application Information
AI Technical Summary
Problems solved by technology
Method used
Image
Examples
preparation example Construction
[0037] The preparation method of silicon dioxide micropowder composition, concrete steps are as follows:
[0038] According to the parts by weight of Table 1, the rounded silica micropowder, spherical silica micropowder, angular silica micropowder, ultrafine silica micropowder and fused silica micropowder are put into a high-speed mixer for mixing, and The time is 15min, the mixing temperature is 90°C, after mixing, add the surface treatment agent γ-aminopropyltriethoxysilane (KH550), the modification temperature is 120°C, the modification time is 10min, after the modification is completed, cool to room temperature , and sieved to obtain a silicon dioxide micropowder composition with a certain particle size distribution.
[0039] The composition of silicon dioxide micropowder composition in each embodiment of table 1 and comparative example
[0040]
[0041] The fluidity of the silicon dioxide micropowder composition in each embodiment and comparative example is according ...
Embodiment 1
[0051] Comparing Example 1 and Example 3 with Comparative Examples 12 and 13, it is found that the more spherical silica powder is added, the better the fluidity performance and the worse the thermal conductivity, but the increase in spherical silica powder will lead to higher costs.
Embodiment 5
[0052] Comparing Example 5, Example 6, and Example 7 with Comparative Examples 14 and 15, it is found that the amount of angular silica micropowder is reduced, the thermal conductivity is worse, and the fluidity is better. Controlling the amount of addition is mainly to control costs.
PUM
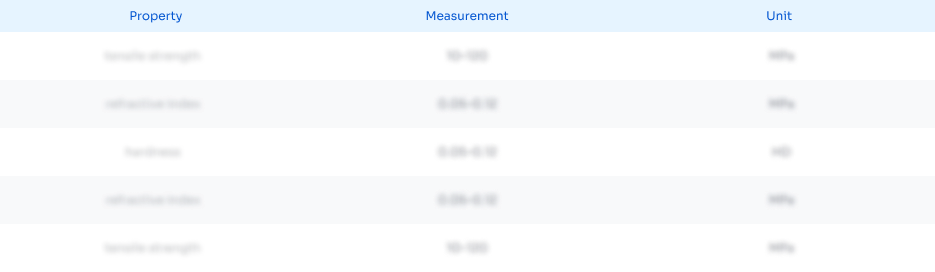
Abstract
Description
Claims
Application Information

- R&D
- Intellectual Property
- Life Sciences
- Materials
- Tech Scout
- Unparalleled Data Quality
- Higher Quality Content
- 60% Fewer Hallucinations
Browse by: Latest US Patents, China's latest patents, Technical Efficacy Thesaurus, Application Domain, Technology Topic, Popular Technical Reports.
© 2025 PatSnap. All rights reserved.Legal|Privacy policy|Modern Slavery Act Transparency Statement|Sitemap|About US| Contact US: help@patsnap.com