Main beam deflection monitoring device based on binocular vision and monitoring method thereof
A monitoring device and a technology for deflection of the main girder, which is applied in the field of cranes, can solve the problems of inward bending, inability to monitor deflection, time-consuming and labor-intensive problems, and achieve the effect of real-time deformation
- Summary
- Abstract
- Description
- Claims
- Application Information
AI Technical Summary
Problems solved by technology
Method used
Image
Examples
Embodiment 1
[0058] Please refer to figure 1 , the crane girder deflection online monitoring device of the present embodiment is suitable for on-line detection of the girder 4 deflection of the gantry crane, which includes a binocular camera 1 and a target 2, wherein the binocular camera 1 is composed of a left camera and a right camera, They are all set on the end beam 3 on one side of the crane, and the target 2 is located on any one of the two main beams 4 of the gantry crane. Due to the stress distribution, usually the most deformed part of the main beam 4 is located in the middle of the main beam 4, so In this embodiment, the target 2 is arranged in the middle of the main beam 4 .
[0059] Target 2 as figure 2 As shown, the background is white, and there are two black positioning rectangles on the white background, wherein the centroid of the first positioning rectangle is A, and the centroid of the second positioning rectangle is B. In this embodiment, for the convenience of illust...
Embodiment 2
[0068] The difference between the on-line monitoring device for the deflection of the main girder 4 of the crane in this embodiment and the first embodiment is that two micro switches are also provided, and the two micro switches are respectively arranged on both sides of the center of the main girder 4. Specifically, the main girder The length of the beam 4 is Z, and it is arranged on both sides of the distance Z / 5 from the center. The deflection of the main beam 4 is only detected when the trolley 5 is operating within the range clamped by the two micro switches.
Embodiment 3
[0070] See Figure 5 , a method for monitoring the deflection of crane girder 4 based on binocular vision of the present embodiment, which includes the following steps,
[0071] Step S1, collecting left camera images and right camera images;
[0072] Step S2, processing the left camera image and the right camera image;
[0073] Step S3, perform three-dimensional reconstruction on the real-time centroid points of the two positioning figures according to the left camera image and the right camera image, and obtain the real-time three-dimensional centroid positions of the first positioning figure and the second positioning figure after real-time reconstruction;
[0074] Step S4. Obtain the real-time deflection value according to the change of the real-time centroid three-dimensional position of the first positioning pattern and the second positioning pattern.
[0075] Wherein, step S2 includes:
[0076] Step S21, correcting the left camera image and the right camera image, and...
PUM
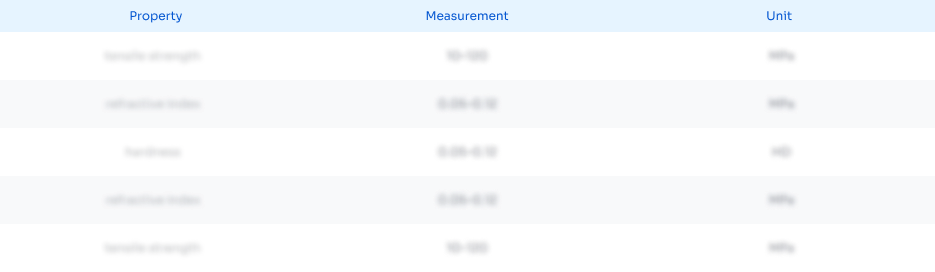
Abstract
Description
Claims
Application Information

- R&D Engineer
- R&D Manager
- IP Professional
- Industry Leading Data Capabilities
- Powerful AI technology
- Patent DNA Extraction
Browse by: Latest US Patents, China's latest patents, Technical Efficacy Thesaurus, Application Domain, Technology Topic, Popular Technical Reports.
© 2024 PatSnap. All rights reserved.Legal|Privacy policy|Modern Slavery Act Transparency Statement|Sitemap|About US| Contact US: help@patsnap.com