Preparation method of hollow grid structure wing rudder
A grid structure, wing rudder technology, applied in the direction of offensive equipment, projectiles, weapon types, etc., can solve the problems of poor wing rudder performance and complex process, and achieve the effects of high forming efficiency, simple steps, and low implementation difficulty.
- Summary
- Abstract
- Description
- Claims
- Application Information
AI Technical Summary
Problems solved by technology
Method used
Image
Examples
preparation example Construction
[0040] The invention provides a method for preparing a wing rudder with a hollow grid structure, the preparation method comprising:
[0041] a. According to the wing rudder structure, the wing rudder is divided into two symmetrical parts up and down along the chord plane, and the upper grid plate model and the lower grid plate model are designed;
[0042] b. According to the design model, prepare the upper grid plate 1 and the lower grid plate 2, such as Figure 1-2 shown;
[0043] c. After assembling the upper grid plate 1 and the lower grid plate 2, carry out diffusion connection, such as image 3 and Figure 5 shown.
[0044] It should be noted that, in the present invention, the chord plane refers to the middle plane between the upper plane and the lower plane of the wing rudder, that is, Figure 7 The C-C side in . The hollow grid structure refers to a structure formed by interlacing reinforcing ribs inside the rudder, and there is no particular limitation on this st...
Embodiment 1
[0076] a. According to the wing rudder structure (chord length 500mm, span length 400mm, maximum thickness t at the root 1 = 32mm, rib width 1.5mm, material is Ti2AlNb), the rib includes a notch with a depth of 0.5mm and a width of 1.5mm, the notch is located in the middle of the rib, and the wing rudder is divided into two symmetrical parts up and down along the chord plane , to design the upper grid plate model and the lower grid plate model;
[0077] b. Prepare the upper grid plate and the lower grid plate by mechanical processing according to the design model, the thickness is 17mm (α is 2), the diameter of the guide hole of the upper grid plate and the lower grid plate is 20mm, and the blind hole of the lower grid plate 12mm deep;
[0078] Machining prepares guide post (material is Ti2AlNb), and guide post is long 25mm, and the diameter of guide post is 20mm;
[0079] The gaps on the ribs of the upper and lower grid plates are distributed in the middle of the ribs, with...
Embodiment 2
[0087] a. According to the wing rudder structure (chord length 450mm, span length 400mm, maximum thickness t at the root 1 = 40mm, rib width 1.2mm, material is Ti2AlNb), divide the wing rudder into two symmetrical parts up and down along the chord plane, and design the upper grid plate model and the lower grid plate model;
[0088] b. Prepare the upper grid plate and the lower grid plate by mechanical processing according to the design model, the thickness is 22mm (α is 4), the diameter of the guide hole of the upper grid plate and the lower grid plate is 25mm, and the blind hole of the lower grid plate 15mm deep;
[0089] The guide post (material is Ti2AlNb) is prepared by machining. The length of the guide post is 35mm, and the diameter of the guide post is 25mm. The negative difference is taken during processing, and the maximum negative difference is -0.5.
[0090] The gaps on the reinforcing ribs of the upper and lower grid plates are 0.7mm deep and 2mm wide; the opening...
PUM
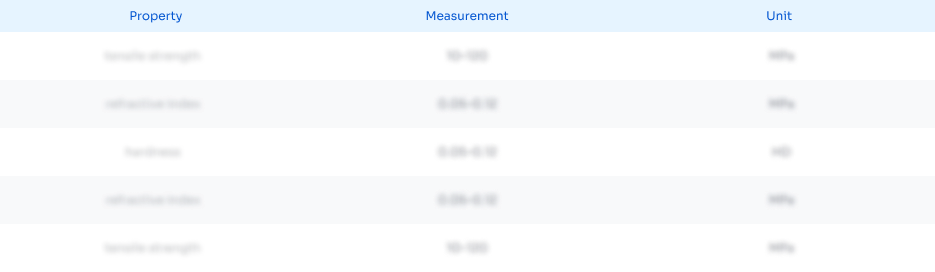
Abstract
Description
Claims
Application Information

- R&D Engineer
- R&D Manager
- IP Professional
- Industry Leading Data Capabilities
- Powerful AI technology
- Patent DNA Extraction
Browse by: Latest US Patents, China's latest patents, Technical Efficacy Thesaurus, Application Domain, Technology Topic, Popular Technical Reports.
© 2024 PatSnap. All rights reserved.Legal|Privacy policy|Modern Slavery Act Transparency Statement|Sitemap|About US| Contact US: help@patsnap.com