Large component collaborative machining planning method for multi-robot collision avoidance coupling planning problem
A multi-robot and robot technology, which is applied in the field of large-part collaborative processing planning for multi-robot collision avoidance coupling planning problem, can solve the problems of large end effector, affecting the application of ILS algorithm, and difficulty in efficient local optimization. Cope with the complexity of the problem, speed up the optimization, and achieve good results
- Summary
- Abstract
- Description
- Claims
- Application Information
AI Technical Summary
Problems solved by technology
Method used
Image
Examples
Embodiment
[0119] There are currently four processing robots working together to process a continuous area on the surface of a large component. Discrete processing tasks are distributed in the area, and the tasks are not evenly distributed; the four robots are equipped with end effectors of the same specification and have a non-negligible volume. The end effector can process one task at a time. Each robot covers a part of the tasks in the processing area, and the work envelopes of the robots overlap.
[0120]The problem to be solved is: how to assign tasks to the four robots and specify the processing process of each robot, so that the time for the robots to complete all processing tasks is the shortest without any collisions in the middle.
[0121] The present invention proposes a partition-based multi-robot collaborative processing planning method for large parts, including the following content:
[0122] Step 1. According to the distribution of processing tasks and constrained by the...
PUM
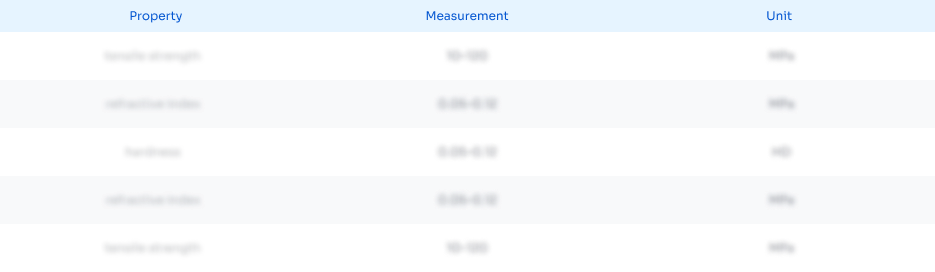
Abstract
Description
Claims
Application Information

- R&D Engineer
- R&D Manager
- IP Professional
- Industry Leading Data Capabilities
- Powerful AI technology
- Patent DNA Extraction
Browse by: Latest US Patents, China's latest patents, Technical Efficacy Thesaurus, Application Domain, Technology Topic, Popular Technical Reports.
© 2024 PatSnap. All rights reserved.Legal|Privacy policy|Modern Slavery Act Transparency Statement|Sitemap|About US| Contact US: help@patsnap.com