Method for remarkably improving critical current density of Bi2212 superconducting material
A critical current density, bi2212 technology, applied in the field of high temperature superconducting material preparation, can solve the problems of uncontrollable AEC phase content, unrealized, undirected control, etc., to achieve strong controllability and operability, low cost, promotion The effect of grain growth
- Summary
- Abstract
- Description
- Claims
- Application Information
AI Technical Summary
Problems solved by technology
Method used
Examples
Embodiment 1
[0023] This embodiment includes the following steps:
[0024] Step 1. The AEC phase of 14:24 is artificially prepared by co-precipitation process; the mass ratio of Sr, Ca, and Cu in the AEC phase of 14:24 has an error range of less than 3% compared with the design mass ratio; the co-precipitation process The specific process is: preparation of oxalic acid ethanol solution, and then SrCO 3 , CaCO 3 and Cu are dissolved in nitric acid to obtain a nitrate mixed solution, wherein the atomic ratio of (Sr+Ca) to Cu is 14:24, and the atomic ratio of Sr to Ca is 0.45:0.55, and the mixed solution of nitrate and ammonia water are added simultaneously The co-precipitated powder was obtained from the oxalic acid ethanol solution, and after the co-precipitated powder was cracked and ground step by step, the AEC phase of 14:24 was obtained;
[0025] Step 2. Add the 14:24 AEC phase obtained in step 1 to the Bi2212 powder and stir and mix evenly to obtain a mixed powder; the added mass of ...
Embodiment 2
[0031] This embodiment includes the following steps:
[0032]Step 1, artificially prepare and obtain the AEC phase of 14:24 by spray pyrolysis process; the mass ratio of Sr, Ca, and Cu in the AEC phase of 14:24 is less than 3% in the error range of the design mass ratio; the spray thermal The specific process of the solution process is: the SrCO 3 , CaCO 3 and Cu are dissolved in nitric acid to obtain a mixed solution of nitrate, wherein the atomic ratio of (Sr+Ca) to Cu is 14:24, and the atomic ratio of Sr to Ca is 0.45:0.55, and then the mixed solution of nitrate is sprayed Pyrolysis to obtain pyrolysis powder, after pyrolysis powder is cracked and ground step by step, the AEC phase of 14:24 is obtained;
[0033] Step 2. Add the 14:24 AEC phase obtained in step 1 to the Bi2212 powder and stir and mix evenly to obtain a mixed powder; the added mass of the 14:24 AEC phase is 3% of the mass of the Bi2212 powder;
[0034] Step 3, prepare slurry with the mixed powder obtained ...
Embodiment 3
[0039] This embodiment includes the following steps:
[0040] Step 1, artificially prepare and obtain the AEC phase of 14:24 by spray pyrolysis process; the mass ratio of Sr, Ca, and Cu in the AEC phase of 14:24 is less than 3% in the error range of the design mass ratio; the spray thermal The specific process of the solution process is: the SrCO 3 , CaCO 3 and Cu are dissolved in nitric acid to obtain a mixed solution of nitrate, wherein the atomic ratio of (Sr+Ca) to Cu is 14:24, and the atomic ratio of Sr to Ca is 0.45:0.55, and then the mixed solution of nitrate is sprayed Pyrolysis to obtain pyrolysis powder, after pyrolysis powder is cracked and ground step by step, the AEC phase of 14:24 is obtained;
[0041] Step 2. Add the 14:24 AEC phase obtained in Step 1 to the Bi2212 powder and stir and mix evenly to obtain a mixed powder; the added mass of the 14:24 AEC phase is 5% of the mass of the Bi2212 powder;
[0042] Step 3, prepare slurry with the mixed powder obtained...
PUM
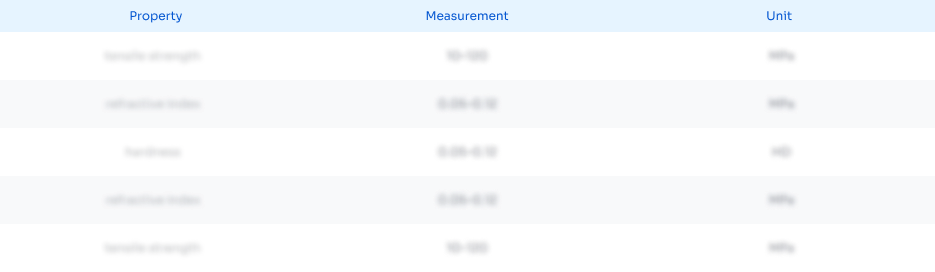
Abstract
Description
Claims
Application Information

- Generate Ideas
- Intellectual Property
- Life Sciences
- Materials
- Tech Scout
- Unparalleled Data Quality
- Higher Quality Content
- 60% Fewer Hallucinations
Browse by: Latest US Patents, China's latest patents, Technical Efficacy Thesaurus, Application Domain, Technology Topic, Popular Technical Reports.
© 2025 PatSnap. All rights reserved.Legal|Privacy policy|Modern Slavery Act Transparency Statement|Sitemap|About US| Contact US: help@patsnap.com