Hydraulic motor control device and method based on DSP
A technology of hydraulic motors and control devices, which is applied in the direction of fluid pressure actuators, program control, computer control, etc., can solve problems such as poor stability and complicated control process, achieve accurate control, simplify control process, and improve control stability. Effect
- Summary
- Abstract
- Description
- Claims
- Application Information
AI Technical Summary
Problems solved by technology
Method used
Image
Examples
Embodiment 1
[0066] see figure 1 A DSP-based hydraulic motor control device described in this embodiment is described. The control system is implemented based on DSP and is used to drive and control the hydraulic motor shaft in the electro-hydraulic servo system; the DSP includes a first-order feed-forward module 1, a second-order Order feedforward module 2, parallel integral module 3, position compensator 4, speed compensator 5, acceleration compensator 6, differential pressure compensator 7, analog-to-digital converter 8, state observer 9, No. 1 subtractor 10, 1 No. adder 11, No. 2 subtractor 12, No. 3 subtractor 13 and No. 4 subtractor 14;
[0067] The input end of the first-order feedforward module 1 is used to receive a given angular velocity of the hydraulic motor shaft, and the output end of the first-order feedforward module 1 is connected to the first adder input end of the No. 1 adder 11;
[0068] The input end of the second-order feedforward module 2 is used to receive the give...
Embodiment 2
[0111] For details, see figure 1 , using the control method realized by a DSP-based hydraulic motor control device, the control method includes the following process:
[0112] Step S1, the first-order feedforward module 1 compensates the given angular velocity of the hydraulic motor shaft received by it, and sends the given angular velocity compensation result to the first addend input terminal of the No. 1 adder 11;
[0113] The second-order feedforward module 2 compensates the given angular acceleration of the hydraulic motor shaft received by it, and sends the given angular acceleration compensation result to the first minuend input terminal of the No. 3 subtractor 13;
[0114] After the given angular position of the hydraulic motor shaft received by No. 1 subtractor 10 is different from the measured angular position, the obtained angular position deviation is simultaneously sent to the parallel integration module 3 and the position compensator 4, wherein the parallel integ...
PUM
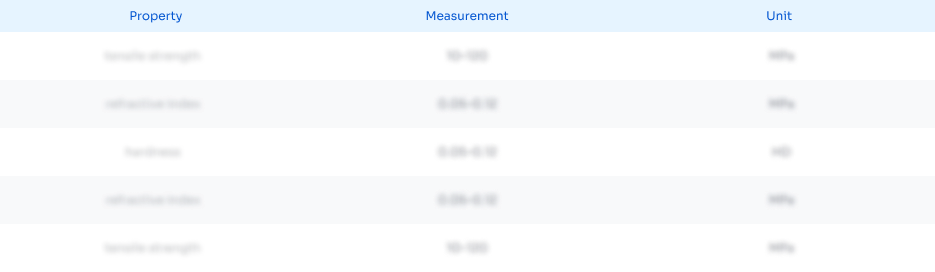
Abstract
Description
Claims
Application Information

- R&D Engineer
- R&D Manager
- IP Professional
- Industry Leading Data Capabilities
- Powerful AI technology
- Patent DNA Extraction
Browse by: Latest US Patents, China's latest patents, Technical Efficacy Thesaurus, Application Domain, Technology Topic, Popular Technical Reports.
© 2024 PatSnap. All rights reserved.Legal|Privacy policy|Modern Slavery Act Transparency Statement|Sitemap|About US| Contact US: help@patsnap.com