Method for synthesizing ultrahigh-viscosity water-soluble block polyether by one-pot method
A block polyether, water-soluble technology, applied in the field of anode materials for sodium-ion batteries, can solve the problems of product viscosity drop, molecular weight not meeting the expected requirements, product turbidity, etc., and achieve the goal of increasing viscosity, increasing molecular weight, and reducing reaction rate Effect
- Summary
- Abstract
- Description
- Claims
- Application Information
AI Technical Summary
Problems solved by technology
Method used
Examples
specific Embodiment 1
[0024] Step 1: Place the compound containing active hydrogen in a reaction kettle containing 9.21g (containing 0.3mol of hydroxyl) glycerol and 9g (containing 0.1mol of hydroxyl) propylene glycol monomethyl ether initial polyether, and add 2‰wt phosphazene Catalyst, which catalyzes the nucleophilic substitution reaction between the active hydrogen and the initial polyether. After vacuuming, the temperature in the reactor is raised to 130°C to ensure that the water content is within 0.1%wt, and an initiator with a total hydroxyl mole number of 0.4mol is obtained;
[0025] Step 2: Introduce a mixture of 792g (18mol) ethylene oxide and 5220g (50mol) propylene oxide into the reactor, so that the mixture of ethylene oxide and propylene oxide and the active hydrogen in the initiator will undergo nucleophilicity Substitution reaction to generate a new structure with active hydrogen, and the new structure with active hydrogen continues to undergo epoxy ring reaction with the mixture of...
specific Embodiment 2
[0030] Step 1: Put the compound containing active hydrogen in the initial polyether reaction kettle containing 7.6g 1,2-propanediol (containing 0.2mol of hydroxyl) and 26.4g of propylene glycol monobutyl ether (containing 0.2mol of hydroxyl), and add 2‰wt Phosphazene catalyst, which catalyzes the nucleophilic substitution reaction between the active hydrogen and the initial polyether. After vacuuming, the temperature in the reactor is raised to 150°C to ensure that the water content is within 0.1%wt, and the total molar number of hydroxyl groups is 0.4mol. agent;
[0031] Step 2: Introduce a mixture of 1584g (36mol) ethylene oxide and 2088g (36mol) propylene oxide into the reactor, so that the mixture of ethylene oxide and propylene oxide and the active hydrogen in the initiator will undergo nucleophilicity Substitution reaction to generate a new structure with active hydrogen, and the new structure with active hydrogen continues to undergo epoxy ring reaction with the mixture...
specific Embodiment 3
[0036] Step 1: Put the compound containing active hydrogen in the initial polyether reaction kettle containing 7.6g 1,2-propanediol (containing 0.2mol of hydroxyl) and 26.4g of propylene glycol monobutyl ether (containing 0.2mol of hydroxyl), and add 2‰wt Phosphazene catalyst, catalyzing the nucleophilic substitution reaction between the active hydrogen and the initial polyether. After vacuuming, the temperature in the reactor is raised to 140°C to ensure that the water content is within 0.1%wt, and the total molar number of hydroxyl groups is 0.4mol. agent;
[0037]Step 2: Introduce a mixture of 1320g (30mol) ethylene oxide and 2320g (30mol) propylene oxide into the reaction kettle to make the mixture of ethylene oxide and propylene oxide react with the active hydrogen in the initiator for nucleophilicity Substitution reaction to generate a new structure with active hydrogen, and the new structure with active hydrogen continues to undergo epoxy ring reaction with the mixture ...
PUM
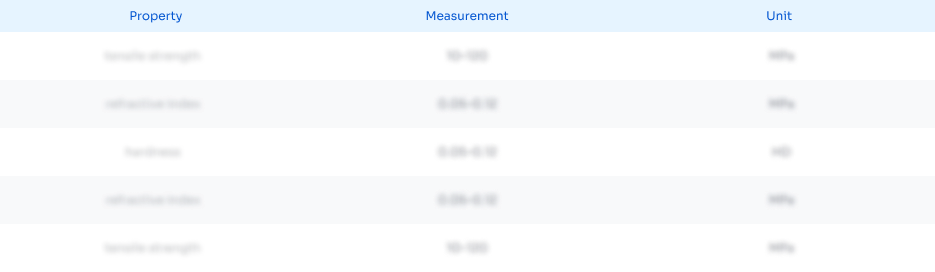
Abstract
Description
Claims
Application Information

- R&D
- Intellectual Property
- Life Sciences
- Materials
- Tech Scout
- Unparalleled Data Quality
- Higher Quality Content
- 60% Fewer Hallucinations
Browse by: Latest US Patents, China's latest patents, Technical Efficacy Thesaurus, Application Domain, Technology Topic, Popular Technical Reports.
© 2025 PatSnap. All rights reserved.Legal|Privacy policy|Modern Slavery Act Transparency Statement|Sitemap|About US| Contact US: help@patsnap.com