Mineral substance volcanic rock fire-resistant bus
A volcanic rock and mineral technology, applied in the direction of cable/conductor manufacturing, conductors, electrical components, etc., can solve the problem that the refractory busbar cannot adapt to various environments, and achieve the effect of saving electricity, saving economic costs and high fire resistance
- Summary
- Abstract
- Description
- Claims
- Application Information
AI Technical Summary
Problems solved by technology
Method used
Examples
Embodiment 1
[0019] A mineral volcanic rock refractory busbar, comprising the following steps:
[0020] Raw material composition: epoxy resin 20kg, curing agent 10kg, volcanic rock 20kg, zirconia powder 20kg, chromium oxide powder 20kg and quartz sand 10kg;
[0021] Stirring steps: Pour 10kg of epoxy resin into the mixer and stir for 2 minutes to make the raw materials in the epoxy resin uniform. After completion, pour 5kg of curing agent into the mixer and stir for 2 minutes to make the epoxy resin and curing agent Mix evenly, and the epoxy resin can be cross-linked and cured by the curing agent. After completion, pour 10kg of volcanic rock into the mixer and stir for 1 minute to make the epoxy resin, curing agent and volcanic rock evenly mixed. Due to the volcanic rock, it will not Any chemical reaction occurs. After completion, pour 10kg of zirconia powder into the mixer and stir for 1 minute to mix epoxy resin, curing agent, volcanic rock and zirconia powder evenly. After completion, p...
Embodiment 2
[0024] A mineral volcanic rock refractory busbar, comprising the following steps:
[0025] Raw material composition: epoxy resin 25kg, curing agent 12.5kg, volcanic rock 25kg, zirconia powder 25kg, chromium oxide powder 25kg and quartz sand 12.5kg;
[0026]Stirring steps: Pour 12.5kg of epoxy resin into the mixer and stir for 3 minutes to make the raw materials in the epoxy resin uniform. After completion, pour 6.25kg of curing agent into the mixer and stir for 3 minutes to make the epoxy resin and The curing agent is evenly mixed, and the epoxy resin can be cross-linked and cured through the curing agent. After completion, pour 12.5kg of volcanic rock into the mixer and stir for 1 minute and 30 seconds to make the epoxy resin, curing agent and volcanic rock evenly mixed. The reason is that there will be no chemical reaction. After the completion, pour 12.5kg of zirconia powder into the mixer and stir for 1 minute and 30 seconds to mix the epoxy resin, curing agent, volcanic r...
Embodiment 3
[0029] A mineral volcanic rock refractory busbar, comprising the following steps:
[0030] Raw material composition: 30kg of epoxy resin, 15kg of curing agent, 30kg of volcanic rock, 30kg of zirconia powder, 30kg of chromium oxide powder and 15kg of quartz sand;
[0031] Stirring steps: Pour 15kg of epoxy resin into the mixer and stir for 4 minutes to make the raw materials in the epoxy resin even. After completion, pour 7.5kg of curing agent into the mixer and stir for 4 minutes to make the epoxy resin The epoxy resin can be cross-linked and cured through the curing agent. After completion, pour 15kg of volcanic rock into the mixer and stir for 2 minutes to make the epoxy resin, curing agent and volcanic rock evenly mixed. The volcanic rock does not Any chemical reaction will occur. After the completion, pour 15kg of zirconia powder into the mixer and stir for 2 minutes to make the epoxy resin, curing agent, volcanic rock and zirconia powder evenly mixed. After completion, po...
PUM
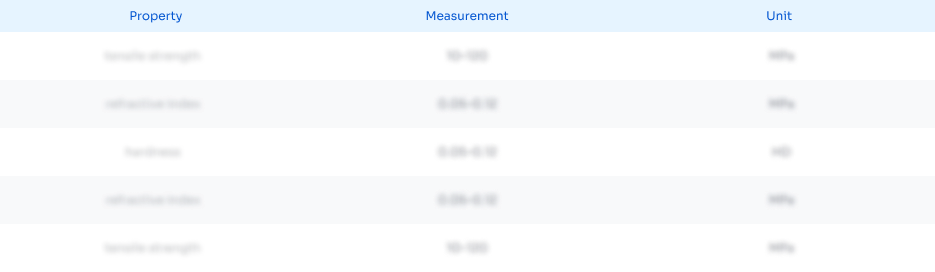
Abstract
Description
Claims
Application Information

- Generate Ideas
- Intellectual Property
- Life Sciences
- Materials
- Tech Scout
- Unparalleled Data Quality
- Higher Quality Content
- 60% Fewer Hallucinations
Browse by: Latest US Patents, China's latest patents, Technical Efficacy Thesaurus, Application Domain, Technology Topic, Popular Technical Reports.
© 2025 PatSnap. All rights reserved.Legal|Privacy policy|Modern Slavery Act Transparency Statement|Sitemap|About US| Contact US: help@patsnap.com