Method for calculating micro-mechanical parameters of reinforced tailings based on PFC discrete element
A technology of mesomechanical parameters and calculation methods, applied in CAD numerical modeling, electrical digital data processing, design optimization/simulation, etc., can solve problems such as few correlation studies of linear contact models, and achieve improved calculation methods and results Accurate, computationally efficient results
- Summary
- Abstract
- Description
- Claims
- Application Information
AI Technical Summary
Problems solved by technology
Method used
Image
Examples
Embodiment Construction
[0018] The present invention will be further described below in conjunction with examples and accompanying drawings, but the embodiments of the present invention are not limited thereto.
[0019] The macroscopic mechanical parameters obtained through the indoor direct shear test are substituted into the model direct shear test, and the mesoscopic mechanical parameters are determined according to the relationship between the macroscopic mechanical parameters and the mesoscopic mechanical parameters, which is the calibration process of the mesoscopic mechanical parameters. The results of the direct shear test were compared with those of the indoor direct shear test. The process of calibrating the mesoscopic parameters is as follows: figure 1 shown.
[0020] The direct shear test model adopts the two-dimensional shear test model in PFC discrete element software. The two-dimensional shear test model is composed of 8 wall units and 2 wing wall units. The internal tailings sand and ...
PUM
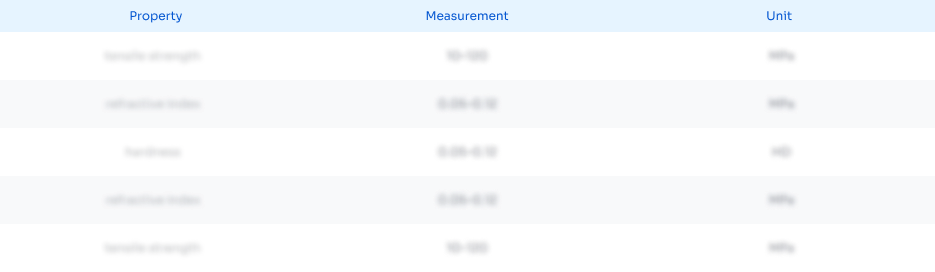
Abstract
Description
Claims
Application Information

- R&D
- Intellectual Property
- Life Sciences
- Materials
- Tech Scout
- Unparalleled Data Quality
- Higher Quality Content
- 60% Fewer Hallucinations
Browse by: Latest US Patents, China's latest patents, Technical Efficacy Thesaurus, Application Domain, Technology Topic, Popular Technical Reports.
© 2025 PatSnap. All rights reserved.Legal|Privacy policy|Modern Slavery Act Transparency Statement|Sitemap|About US| Contact US: help@patsnap.com