Method for efficiently recycling manganese in zinc anode mud in short process
A technology of zinc anode slime and short process, which is applied to the improvement of process efficiency, instruments, optics, etc., can solve the problems of high leaching cost, pollute the environment, and difficult to handle, and achieve the effect of fast reduction reaction rate
- Summary
- Abstract
- Description
- Claims
- Application Information
AI Technical Summary
Problems solved by technology
Method used
Image
Examples
Embodiment 1
[0024] This example provides a short-process high-efficiency recycling method for manganese in zinc anode slime, mainly using the zinc calcined sand neutral leachate in the hydrometallurgy system as the zinc anode mud agent, and adopting hydromelting zinc after pulping SO contained in the roasted zinc concentrate in the system 2 The flue gas reduces the manganese dioxide in zinc anode slime to soluble Mn 2+ . The composition of the zinc anode slime used in this example is shown in Table 1, and the pH of the zinc calcine neutral leach solution is 5.0.
[0025] Table 1 Composition of zinc anode slime
[0026] element mn Zn Pb Fe content(%) 33.26 5.09 1.09 0.13
[0027] like figure 1 As shown, the specific process of the method is:
[0028] (1) First-level pulping. The neutral leaching solution of zinc calcined sand and zinc anode slime are mixed and stirred evenly, the range of liquid-solid weight ratio is controlled at 4:1, the initial pH=3 ...
Embodiment 2
[0033] This example provides a short-process high-efficiency recycling method for manganese in zinc anode slime. The composition of the zinc anode slime used is shown in Table 2, and the pH of the neutral leach solution is 4.8.
[0034] Table 2
[0035] element mn Zn Pb Fe content(%) 33.26 5.09 1.09 0.13
[0036] like figure 1 As shown, the specific process of the method is:
[0037] (1) First-level pulping. The neutral leaching solution of zinc calcined sand and zinc anode slime are mixed and stirred evenly, the liquid-solid ratio range is controlled at 6:1, the initial pH=3, and the mixing time is 45 minutes.
[0038] (2) First order reduction reaction. The prepared pulp is sent to the first-stage reduction reaction kettle, and the flue gas containing sulfur dioxide obtained from the roasting of zinc concentrate reacts with the pulp in contact, and the intake of SO 2 The concentration is controlled at 179g / m 3 , pH=2.0, reaction time 2h, ...
Embodiment 3
[0042] This example provides a short-process high-efficiency recycling method for manganese in zinc anode slime. The composition of the zinc anode slime used is shown in Table 3, and the pH of the neutral leach solution is 4.8.
[0043] table 3
[0044] element mn Zn Pb Fe content(%) 39.55 2.64 2.36 0.12
[0045] like figure 1 As shown, the specific process of the method is:
[0046] (1) First-level pulping. The neutral leaching solution of zinc calcined sand and zinc anode slime are mixed and stirred evenly, the liquid-solid ratio range is controlled at 8:1, the initial pH=3, and the mixing time is 30 minutes.
[0047] (2) First order reduction reaction. The prepared pulp is sent to the first-stage reduction reaction kettle, and the flue gas containing sulfur dioxide obtained from the roasting of zinc concentrate reacts with the pulp in contact, and the intake of SO 2 The concentration is controlled at 162g / m 3 , pH=2.5, reaction time 3h, ...
PUM
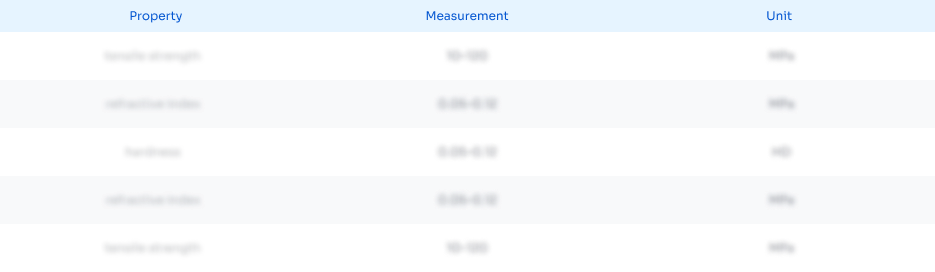
Abstract
Description
Claims
Application Information

- R&D
- Intellectual Property
- Life Sciences
- Materials
- Tech Scout
- Unparalleled Data Quality
- Higher Quality Content
- 60% Fewer Hallucinations
Browse by: Latest US Patents, China's latest patents, Technical Efficacy Thesaurus, Application Domain, Technology Topic, Popular Technical Reports.
© 2025 PatSnap. All rights reserved.Legal|Privacy policy|Modern Slavery Act Transparency Statement|Sitemap|About US| Contact US: help@patsnap.com