Manufacturing method of novel environment-friendly concrete
An environmentally friendly concrete and manufacturing method technology, applied in ceramic products, sustainable waste treatment, application, etc., can solve the problems of shoddy, fake fly ash, waste of water resources, etc., to improve corrosion resistance and crack resistance performance, improved resource utilization, and shortened setting time
- Summary
- Abstract
- Description
- Claims
- Application Information
AI Technical Summary
Problems solved by technology
Method used
Examples
Embodiment 1
[0020] Embodiment 1: a kind of preparation method of novel environment-friendly concrete comprises the following steps:
[0021] Step 1. Select the following raw materials according to the weight ratio: 160 catties of waste water, 13 catties of zeolite powder, 80 catties of composite silicate white cement, 28 catties of fly ash, 12 catties of mica powder, 8 catties of latex powder, 12 catties of wood fiber, 16 catties of vanadium iron slag, 60 catties of gypsum powder, 3 kg of lignosulfonate water reducing agent and 3 catties of vegetable protein foaming agent;
[0022] Step 2. Mix and stir the plant protein foam agent and waste water at a ratio of 1:45 for 20 minutes to obtain mixture A;
[0023] Step 3: Mix and stir fly ash, mica powder, zeolite powder, ferrovanadium slag, gypsum powder and composite Portland white cement for 10 minutes, then add remaining waste water and continue stirring for 20 minutes to obtain mixture B;
[0024] Step 4, then mix and stir obtained mixtur...
Embodiment 2
[0026] Embodiment 2: a kind of preparation method of novel environment-friendly concrete comprises the following steps:
[0027] Step 1. Select the following raw materials according to the weight ratio: 200 catties of waste water, 10 catties of zeolite powder, 70 catties of composite silicate white cement, 33 catties of fly ash, 14 catties of mica powder, 6 catties of latex powder, 10 catties of wood fiber, 20 catties of vanadium iron slag, 50 catties of gypsum powder, 7 catties of polycyclic aromatic salt water reducing agent and 1 catties of aluminum powder foaming agent;
[0028] Step 2: Mix and stir the aluminum powder foam agent and waste water at a ratio of 1:45 for 23 minutes to obtain a mixture A;
[0029] Step 3: Mix and stir fly ash, mica powder, zeolite powder, ferrovanadium slag, gypsum powder and composite Portland white cement for 13 minutes, then add remaining waste water and continue stirring for 23 minutes to obtain mixture B;
[0030] Step 4, then mixing and ...
Embodiment 3
[0032] Embodiment 3: a kind of preparation method of novel environment-friendly concrete comprises the following steps:
[0033] Step 1. Select the following raw materials according to the weight ratio: 180 catties of waste water, 12 catties of zeolite powder, 75 catties of composite silicate white cement, 30 catties of fly ash, 13 catties of mica powder, 7 catties of latex powder, 11 catties of wood fiber, 18 catties of ferrovanadium slag, 55 catties of gypsum powder, 5 catties of water-soluble resin sulfonate water reducing agent and 2 catties of rosin acid soap foaming agent;
[0034] Step 2, mix the rosin acid soap foam agent and waste water in a ratio of 1:45 and stir for 25 minutes to obtain the mixture A;
[0035] Step 3: Mix and stir fly ash, mica powder, zeolite powder, ferrovanadium slag, gypsum powder and composite Portland white cement for 15 minutes, then add remaining waste water and continue stirring for 25 minutes to obtain mixture B;
[0036] Step 4, then mixi...
PUM
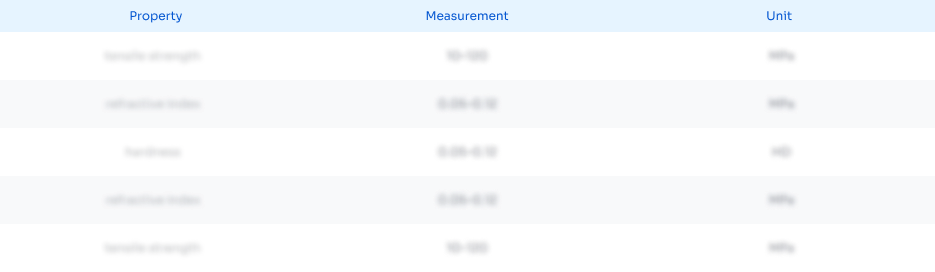
Abstract
Description
Claims
Application Information

- R&D
- Intellectual Property
- Life Sciences
- Materials
- Tech Scout
- Unparalleled Data Quality
- Higher Quality Content
- 60% Fewer Hallucinations
Browse by: Latest US Patents, China's latest patents, Technical Efficacy Thesaurus, Application Domain, Technology Topic, Popular Technical Reports.
© 2025 PatSnap. All rights reserved.Legal|Privacy policy|Modern Slavery Act Transparency Statement|Sitemap|About US| Contact US: help@patsnap.com