Milling force measuring instrument based on thin film strain gauge
A strain gauge and measuring instrument technology, which is used in measuring/indicating equipment, metal processing mechanical parts, metal processing equipment, etc., can solve the problem of difficult to measure the weak strain signal on the tool holder surface, the weak strain signal on the tool holder surface, hysteresis and creep. and other problems, to achieve the effect of simple structure, wide practical range and convenient manufacturing
- Summary
- Abstract
- Description
- Claims
- Application Information
AI Technical Summary
Problems solved by technology
Method used
Image
Examples
Embodiment Construction
[0030] The present invention will be further described below in conjunction with accompanying drawing and specific embodiment:
[0031] Such as Figure 1 to Figure 7 As shown, a kind of milling force measuring instrument based on thin-film strain gauge provided by the present invention comprises a tool holder, on which an electromechanical device is fixed, and the electromechanical device includes a battery, a thin-film strain gauge, a signal processing circuit and a signal transmitting device, and the batteries are respectively It is electrically connected with the film strain gauge, the signal processing circuit and the signal transmitting device. The battery is responsible for supplying energy, and the thin film strain gauge is responsible for sensing the strain signal on the surface of the tool holder due to the cutting force. The signal processing circuit collects and amplifies the signal measured by the thin film strain gauge, and the signal transmitting device transmits...
PUM
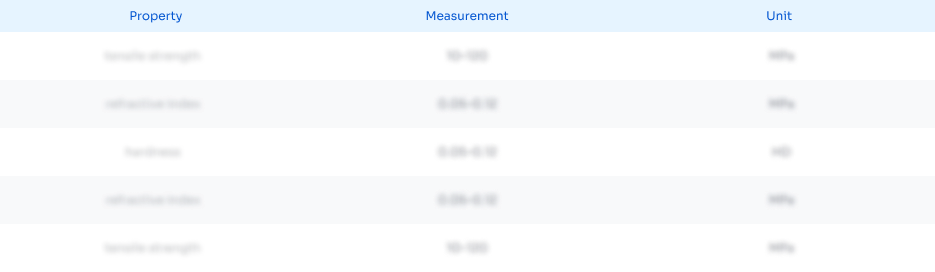
Abstract
Description
Claims
Application Information

- R&D
- Intellectual Property
- Life Sciences
- Materials
- Tech Scout
- Unparalleled Data Quality
- Higher Quality Content
- 60% Fewer Hallucinations
Browse by: Latest US Patents, China's latest patents, Technical Efficacy Thesaurus, Application Domain, Technology Topic, Popular Technical Reports.
© 2025 PatSnap. All rights reserved.Legal|Privacy policy|Modern Slavery Act Transparency Statement|Sitemap|About US| Contact US: help@patsnap.com