Core material, blade and blade forming method
A molding method and core material technology, applied to machines/engines, other household appliances, mechanical equipment, etc., can solve problems such as poor surface quality and strength of structural parts, large differences in penetration speed, waste of raw materials, etc., to avoid waste of resin Raw materials, improving fixed adhesive performance, and avoiding the effect of residual resin
- Summary
- Abstract
- Description
- Claims
- Application Information
AI Technical Summary
Problems solved by technology
Method used
Image
Examples
Embodiment Construction
[0054] The present invention is further illustrated below by means of examples, but the present invention is not limited to the scope of the examples.
[0055] Such as Figure 1-4As shown, a core material 1, the upper surface of the core material 1 is provided with at least one first deep groove 11 and at least one first shallow groove 12 connected to each other, and the first deep groove 11 and the first shallow groove 12 are arranged on the upper surface. Different directions of the surface and extending to the edge of the upper surface, the lower surface of the core material 1 is provided with at least one second deep groove 13 and at least one second shallow groove 14 that communicate with each other, and the second deep groove 13 and the second shallow groove 14 are arranged on the lower surface. Different directions of the surface and extending to the edge of the lower surface, the depth of the first deep groove 11 and the second deep groove 13 is 1 / 3 to 4 / 5 of the thick...
PUM
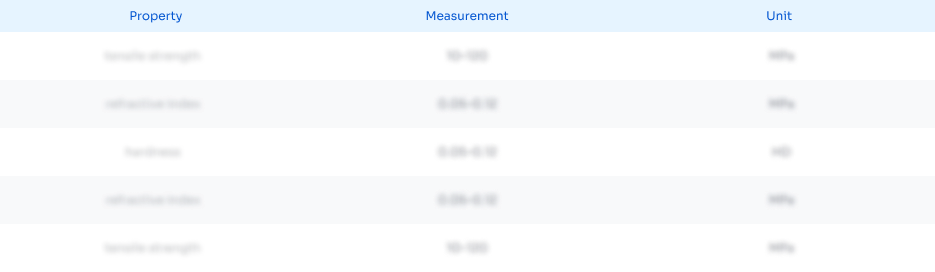
Abstract
Description
Claims
Application Information

- R&D
- Intellectual Property
- Life Sciences
- Materials
- Tech Scout
- Unparalleled Data Quality
- Higher Quality Content
- 60% Fewer Hallucinations
Browse by: Latest US Patents, China's latest patents, Technical Efficacy Thesaurus, Application Domain, Technology Topic, Popular Technical Reports.
© 2025 PatSnap. All rights reserved.Legal|Privacy policy|Modern Slavery Act Transparency Statement|Sitemap|About US| Contact US: help@patsnap.com