Full-automatic numerical control corner splicing machine and corner splicing method thereof
A fully automatic, angle forming machine technology, used in hand-held tools, workpiece clamping devices, manufacturing tools, etc., can solve the problems of prolonged processing time, low internal angle positioning accuracy, lead screw wear, etc., to improve operating efficiency and accuracy. , Accurate and reliable internal angle positioning, eliminating the effect of hydraulic oil temperature rise
- Summary
- Abstract
- Description
- Claims
- Application Information
AI Technical Summary
Problems solved by technology
Method used
Image
Examples
Embodiment Construction
[0037] In order to explain the overall concept of the present invention more clearly, the following will be described in detail by way of examples in conjunction with the accompanying drawings.
[0038] In the following description, many specific details are set forth in order to fully understand the present invention. However, the present invention can also be implemented in other ways different from those described here. Therefore, the protection scope of the present invention is not limited by the specific details disclosed below. EXAMPLE LIMITATIONS.
[0039] Each embodiment in this specification is described in a progressive manner, the same and similar parts of each embodiment can be referred to each other, and each embodiment focuses on the differences from other embodiments.
[0040] In addition, the terms "transverse", "longitudinal", "front and back", "upper end" and the like are used for descriptive purposes only, and should not be construed as indicating or implyin...
PUM
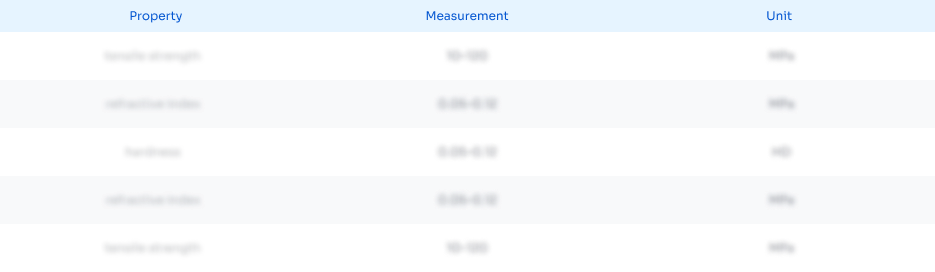
Abstract
Description
Claims
Application Information

- R&D Engineer
- R&D Manager
- IP Professional
- Industry Leading Data Capabilities
- Powerful AI technology
- Patent DNA Extraction
Browse by: Latest US Patents, China's latest patents, Technical Efficacy Thesaurus, Application Domain, Technology Topic, Popular Technical Reports.
© 2024 PatSnap. All rights reserved.Legal|Privacy policy|Modern Slavery Act Transparency Statement|Sitemap|About US| Contact US: help@patsnap.com