Surgical robot, surgical instrument and force transmission device
A technology of transmission device and surgical instrument, applied in the field of medical instruments, can solve the problems of complex transmission structure, low force transmission efficiency, difficult assembly and manufacturing, etc.
- Summary
- Abstract
- Description
- Claims
- Application Information
AI Technical Summary
Problems solved by technology
Method used
Image
Examples
no. 1 example
[0102] image 3 A schematic diagram showing the internal structure of the force transmission device according to the first preferred embodiment of the present invention, Figure 4 A schematic top view of the force transmission device according to the first preferred embodiment of the present invention is shown.
[0103] In the first preferred embodiment of the present invention, a force transmission device is provided, wherein the target motion of the actuation module includes translation along a first direction, and the force transmission module can perform translation along a second direction driven by the moving member. translate in one direction, drive the actuator module to translate in the first direction, and finally drive the telescopic rod 201 to translate in the first direction. In this method, the force transmission device as a whole is in rigid contact, that is, the force transmission device is a rigid component as a whole, so that the power transmission loss betw...
no. 2 example
[0115] Figure 8 A schematic diagram showing the internal structure of the force transmission device according to the second preferred embodiment of the present invention, Figure 9 It shows a schematic top view of the force transmission device according to the second preferred embodiment of the present invention, Figure 10 It shows a front structural schematic view of the force transmission device according to the second preferred embodiment of the present invention.
[0116] In a second preferred embodiment of the present invention there is provided a force transfer device, wherein the target movement of the actuation mass comprises oscillation about a second direction and translation along a first direction, said oscillation about the second direction enabling actuation The translation along the first direction, and the force transmission module can perform the translation along the third direction driven by the moving part, and drive the actuation module to swing around ...
no. 3 example
[0124] Figure 12 A schematic diagram showing the internal structure of the force transmission device according to the third preferred embodiment of the present invention, Figure 13 It shows a schematic top view of the force transmission device according to the third preferred embodiment of the present invention, Figure 14 It shows a schematic structural diagram of the cooperation between the actuating module and the telescopic rod according to the third preferred embodiment of the present invention, Figure 15 for Figure 14 A partial enlargement of the structure.
[0125] In a third preferred embodiment of the present invention, a force transmission device is provided, wherein the target movement of the actuation module includes opening and closing around a first direction, and the force transmission module is configured to be able to is driven to perform translation along the third direction, and drives the actuating module to open and close around the first direction;...
PUM
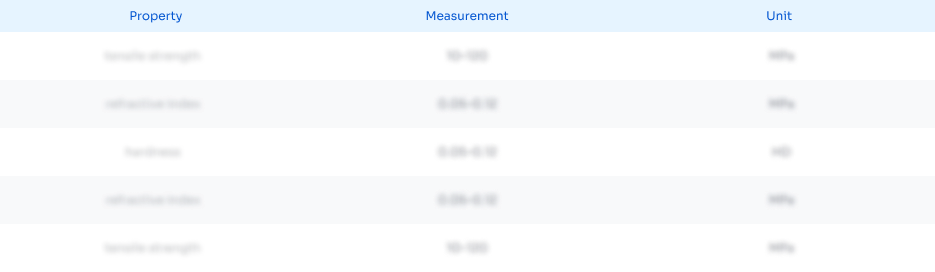
Abstract
Description
Claims
Application Information

- Generate Ideas
- Intellectual Property
- Life Sciences
- Materials
- Tech Scout
- Unparalleled Data Quality
- Higher Quality Content
- 60% Fewer Hallucinations
Browse by: Latest US Patents, China's latest patents, Technical Efficacy Thesaurus, Application Domain, Technology Topic, Popular Technical Reports.
© 2025 PatSnap. All rights reserved.Legal|Privacy policy|Modern Slavery Act Transparency Statement|Sitemap|About US| Contact US: help@patsnap.com