Shaping device for copper wire connectors of automobile wire harness
A technology for shaping devices and automotive wiring harnesses, which is applied in connection, circuit/collector components, electrical components, etc., can solve problems such as low production efficiency, difficulty in ensuring quality stability, and high labor intensity, so as to improve processing efficiency and save energy. The effect of removing the pressing equipment and simplifying the structural design
- Summary
- Abstract
- Description
- Claims
- Application Information
AI Technical Summary
Problems solved by technology
Method used
Image
Examples
Embodiment Construction
[0034] In order to make the technical means, creative features, goals and effects achieved by the present invention easy to understand, the present invention will be further described below in conjunction with specific embodiments.
[0035] Such as Figure 1 to Figure 14 As shown, a shaping device for copper wire joints of automobile wiring harnesses includes a base 1, an overturning assembly 2, a stamping assembly 3, and a side mold assembly 4, and one end of the pressing plate 21 in the overturning assembly 2 is rotatably connected to the side of the base 1 and arranged On the connecting seat 13 of the pedestal, the flipping assembly 2 is connected to the stamping assembly 3 and can be flipped to a horizontal position during the forward movement of the stamping assembly 3, so as to limit the wire harness placed on the base 1 in the vertical direction , the stamping assembly 3 is installed horizontally on the base 1 and cooperates with the side mold assembly 4 to realize simu...
PUM
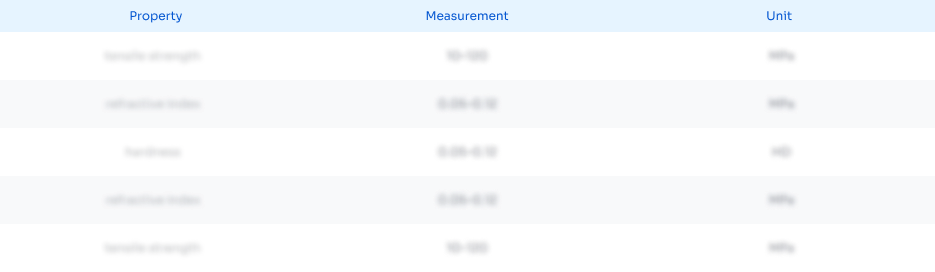
Abstract
Description
Claims
Application Information

- Generate Ideas
- Intellectual Property
- Life Sciences
- Materials
- Tech Scout
- Unparalleled Data Quality
- Higher Quality Content
- 60% Fewer Hallucinations
Browse by: Latest US Patents, China's latest patents, Technical Efficacy Thesaurus, Application Domain, Technology Topic, Popular Technical Reports.
© 2025 PatSnap. All rights reserved.Legal|Privacy policy|Modern Slavery Act Transparency Statement|Sitemap|About US| Contact US: help@patsnap.com