Transparent flame-retardant PMMA resin and preparation method thereof
A resin and transparent technology, applied in the field of polymers, can solve the problems of poor heat resistance of PMMA, failure to meet market demand, PMMA dripping, etc., and achieve long-term flame retardancy, increased cross-linking degree, and avoid migration effects
- Summary
- Abstract
- Description
- Claims
- Application Information
AI Technical Summary
Problems solved by technology
Method used
Image
Examples
Embodiment 1
[0042] Preparation of flame retardant comonomer: Put 300g of phenyl dichlorophosphate, 800g of tetrahydrofuran, and 50g of triethylamine into a three-necked flask with stirring, stir evenly at room temperature and slowly drop in 400g of p-phenol, and raise the temperature to 60°C after the addition is completed After reacting for 12 hours, triethylamine hydrochloride was filtered off after the reaction, and the remaining liquid was distilled under reduced pressure, concentrated to remove most of the residual solvent, then deionized water was added, filtered, and a white solid was precipitated to obtain intermediate C;
[0043] Put 100g of intermediate C, 500g of glycidyl methacrylate, and 1g of potassium hydroxide into the reactor and stir evenly, raise the temperature to 35°C, and react for 5 hours to obtain flame retardant monomer E;
[0044] Preparation of PMMA resin: put 80g of flame retardant monomer E, 800g of methyl methacrylate, 4g of tert-dodecyl mercaptan, and 0.06g o...
Embodiment 2
[0046] Preparation of flame retardant comonomer: put 100g of phenylphosphoryl dichloride, 600g of tetrahydrofuran, and 250g of triethylamine into a three-necked flask with stirring, stir evenly at room temperature and slowly drop in 200g of 4-aminophenol, and heat up after the dropwise addition React at 50°C for 18 hours. After the reaction, triethylamine hydrochloride was filtered off, the remaining liquid was distilled under reduced pressure, concentrated to remove most of the residual solvent, and then deionized water was added, filtered, and a white solid was precipitated to obtain intermediate C;
[0047] Put 30g of intermediate C, 20g of glycidyl methacrylate, and 0.5g of ferric hydroxide into the reactor and stir evenly, raise the temperature to 45°C, and react for 4 hours to obtain flame retardant monomer E;
[0048] Preparation of PMMA resin: Put 10g of flame retardant monomer E, 1200g of methyl methacrylate, 3g of n-octyl mercaptan, and 0.08g of tert-butylperoxy-3,5,5...
Embodiment 3
[0050]Preparation of flame retardant comonomer: 150g of methylphosphoryl dichloride, 1000g of tetrahydrofuran, and 150g of triethylamine were dropped into a three-necked flask with stirring, stirred evenly at room temperature and slowly dripped into 600g of p-carboxyphenol, and the temperature was raised to React at 80°C for 10 hours. After the reaction, triethylamine hydrochloride was filtered off, the remaining liquid was distilled under reduced pressure, concentrated to remove most of the residual solvent, then deionized water was added, filtered, and a white solid was precipitated to obtain intermediate C;
[0051] Put 50g of intermediate C, 100g of glycidyl methacrylate, and 0.3g of potassium carbonate into the reactor and stir evenly, raise the temperature to 55°C, and react for 2 hours to obtain flame retardant monomer E;
[0052] Preparation of PMMA resin: Put 20g of flame retardant monomer E, 1000g of methyl methacrylate, 2g of isooctyl mercaptan, and 0.12g of di-tert-...
PUM
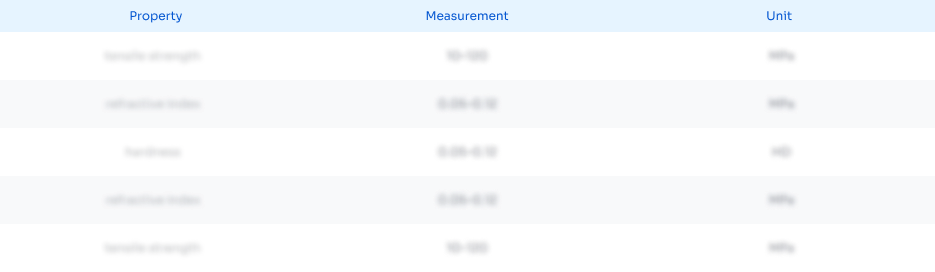
Abstract
Description
Claims
Application Information

- Generate Ideas
- Intellectual Property
- Life Sciences
- Materials
- Tech Scout
- Unparalleled Data Quality
- Higher Quality Content
- 60% Fewer Hallucinations
Browse by: Latest US Patents, China's latest patents, Technical Efficacy Thesaurus, Application Domain, Technology Topic, Popular Technical Reports.
© 2025 PatSnap. All rights reserved.Legal|Privacy policy|Modern Slavery Act Transparency Statement|Sitemap|About US| Contact US: help@patsnap.com