Clamping mechanism of camshaft grinding machine
A technology of clamping mechanism and camshaft, which is applied to the parts of grinding machine tools, abrasive belt grinders, grinding workpiece supports, etc., which can solve the problem that the camshaft is easy to move, affects the machining accuracy of the camshaft, and cannot clamp the camshaft Force adjustment and safety protection and other issues, to achieve effective clamping and smooth rotation, realize flexible processing, and improve the effect of processing accuracy
- Summary
- Abstract
- Description
- Claims
- Application Information
AI Technical Summary
Problems solved by technology
Method used
Image
Examples
Embodiment Construction
[0026] The present invention will be described in detail below in conjunction with accompanying drawing:
[0027] Such as Figure 1-5 Shown:
[0028] A clamping mechanism for a camshaft 3 grinding machine, comprising a headstock 1 and a tailstock 2, wherein the headstock 1 includes a headstock seat 101 and a first servo motor 102, the headstock seat 101 is provided with a transverse headstock hole, and the headstock The headstock main shaft 103 is rotatably connected in the frame hole, and both ends of the headstock main shaft 103 are interference-fitted with rolling bearings 104. Fixed connection, one end of the headstock main shaft 103 passes through the headstock hole and is connected with a reducer 105 through a flat key, the reducer 105 is fixedly connected with the output shaft of the first servo motor 102 through a flat key, and the other end of the headstock main shaft 103 passes through the The head frame hole is fixedly connected to the head frame top 106 through a...
PUM
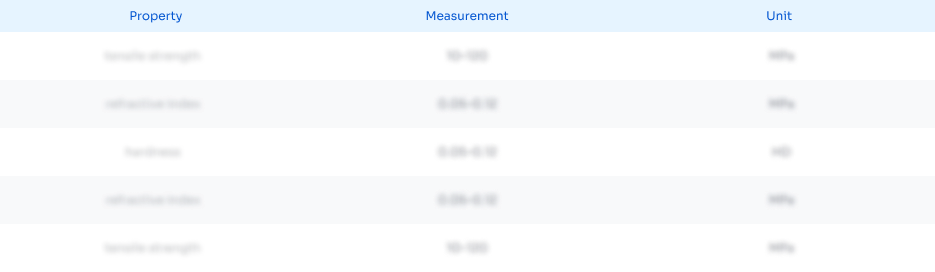
Abstract
Description
Claims
Application Information

- R&D
- Intellectual Property
- Life Sciences
- Materials
- Tech Scout
- Unparalleled Data Quality
- Higher Quality Content
- 60% Fewer Hallucinations
Browse by: Latest US Patents, China's latest patents, Technical Efficacy Thesaurus, Application Domain, Technology Topic, Popular Technical Reports.
© 2025 PatSnap. All rights reserved.Legal|Privacy policy|Modern Slavery Act Transparency Statement|Sitemap|About US| Contact US: help@patsnap.com