Fabric loaded with wool powder and having peculiar smell adsorption function and preparation method thereof
A wool powder and fabric technology, applied in the textile field, can solve problems such as high cost, cumbersome process, and pollution, and achieve stable adsorption performance, wide source of raw materials, and environmental friendliness
- Summary
- Abstract
- Description
- Claims
- Application Information
AI Technical Summary
Problems solved by technology
Method used
Image
Examples
preparation example Construction
[0054] S1. Preparation of wool powder: First, the washed and dried waste wool fabrics were chopped in a shredder with a rotation speed of 2888rpm, and sieved from a 0.25mm mesh to obtain short wool fibers. Then, the wool staple fiber is mixed with deionized water in a certain ratio, and placed in an agitating ball mill for grinding for a certain period of time. After wet milling, wool powder with uniform particle size is collected by spray drying.
[0055] Wool fiber is a complex multi-level structure mainly composed of an outer cuticle, an inner cortex and a cytoplasmic complex connecting the two. Wool is composed of six kinds of chemical bonds (hydrophobic bond, ionic bond, hydrogen bond, isopeptide bond, intermolecular disulfide bond and intramolecular disulfide bond), and is rich in amino and carboxyl functional groups, most of these chemical bonds and functional groups exist in The cortex, and the inert and tight cuticle wraps the cortex, which to a certain extent hinder...
Embodiment 1
[0062] A method for preparing a fabric loaded with wool powder and having an odor absorption function, comprising the following steps:
[0063] S1. Preparation of wool powder: First, the washed and dried waste wool fabrics were chopped in a shredder with a rotation speed of 2888rpm, and sieved from a 0.25mm mesh to obtain short wool fibers. Then, the wool staple fiber was mixed with deionized water at a ratio of 1::10, and placed in a stirring ball mill for grinding for 6 hours. After wet grinding, the wool powder with uniform particle size is collected by spray drying method;
[0064] S2. Configuration of wool emulsion: add the wool powder prepared in step 1 to deionized water at a ratio of 10o.w.f.%, mix and treat until the pH is 4, at a temperature of 40°C and a speed of 600r Under the condition of mechanical stirring for 30 minutes under the condition of 1 / min, a uniformly dispersed wool emulsion can be prepared;
[0065] S3. Compounding of wool powder and fabric. Using...
Embodiment 2~4
[0068] Compared with Embodiment 1, Embodiments 2-4 are different in that the grinding time in step S1 is shown in Table 1, and the others are basically the same as Embodiment 1, and will not be repeated here.
[0069] The processing condition of table 1 embodiment 2~4
[0070]
[0071] see figure 1 As shown, it can be seen from Example 1 and Examples 2-4 that the adsorption rate of untreated wool fiber to ammonia is 53%. The ammonia adsorption capacity of the powder-composite fabric increases significantly when the wool is milled for 6 hours, especially when the fabric is compounded with the powder after ball milling for 6 hours, the ammonia adsorption capacity is the largest, reaching 91% after 60 minutes . This is because the increase of ball milling time promotes the increase of the specific surface area and surface energy of the wool particles, which makes it easier to absorb ammonia quickly and efficiently.
[0072] Therefore, before the fabric is treated in the pre...
PUM
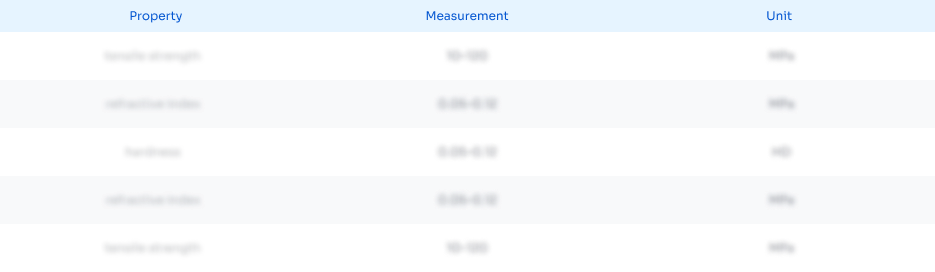
Abstract
Description
Claims
Application Information

- R&D
- Intellectual Property
- Life Sciences
- Materials
- Tech Scout
- Unparalleled Data Quality
- Higher Quality Content
- 60% Fewer Hallucinations
Browse by: Latest US Patents, China's latest patents, Technical Efficacy Thesaurus, Application Domain, Technology Topic, Popular Technical Reports.
© 2025 PatSnap. All rights reserved.Legal|Privacy policy|Modern Slavery Act Transparency Statement|Sitemap|About US| Contact US: help@patsnap.com