Boiler burner arrangement method, lignite boiler and combustion air control method of lignite boiler
A layout method and boiler combustion technology, applied in the boiler field, can solve problems such as the decrease of secondary air momentum, the imbalance of combustion dynamic field organization, and the increase of nitrogen oxide emissions, so as to achieve the effect of eliminating coking and reducing the impact
- Summary
- Abstract
- Description
- Claims
- Application Information
AI Technical Summary
Problems solved by technology
Method used
Image
Examples
Embodiment 1
[0026] Embodiment 1: the following combination figure 1 and figure 2 To illustrate this embodiment, this embodiment provides a method for arranging boiler burners. The four corners of the furnace 1 of the boiler are respectively arranged with burners 2 on the same horizontal plane. The arrangement method includes:
[0027] Each burner 2 is provided with a thick coal powder nozzle 21, a light coal powder nozzle 22 and a secondary air nozzle 23, and the thick coal powder nozzle 21, the light coal powder nozzle 22 and the secondary air Nozzles 23 eject dense-phase pulverized-coal airflow, light-phase pulverized-coal airflow and secondary air in one-to-one correspondence. The central axis and the central axis of the secondary air nozzle 23 are offset on the same side in the horizontal direction to the diagonals of the respective corners of the furnace 1, so that the dense-phase pulverized-coal airflow and the light-phase pulverized-coal airflow converge on The center O of the f...
Embodiment 2
[0033] This implementation provides a lignite boiler that adopts a boiler burner arrangement method described in Embodiment 1, such as figure 1 and figure 2As shown, the four corners of the furnace 1 of the lignite boiler are respectively equipped with burners 2 on the same horizontal plane, and each of the burners 2 is provided with a thick coal powder nozzle 21, a light coal powder nozzle 22 and a secondary air nozzle 23 , the central axis of the thick coal powder nozzle 21, the central axis of the light coal powder nozzle 22 and the central axis of the secondary air nozzle 23 are offset in the center of the furnace 1 on the same side in the horizontal direction, and the The dense coal powder nozzles 21, light coal powder nozzles 22 and secondary air nozzles 23 on the burners 2 at the four corners of the furnace hearth 1 of the lignite burning boiler are arranged in sequence along the circumference of the furnace hearth 1; the light coal powder nozzles The horizontal offse...
Embodiment 3
[0039] This embodiment provides a method for controlling the combustion air of a lignite boiler, which is applied to the lignite boiler described in Example 2. The primary air pulverized coal in the burner is separated by a pulverized coal concentration separator to form the dense phase pulverized coal airflow and The light-phase pulverized-coal airflow, the air volume of the dense-phase pulverized-coal airflow and the air volume of the light-phase pulverized-coal airflow respectively account for 50% of the pulverized-coal air volume of the primary air.
[0040] Further, the percentage of the pulverized coal mass flow rate in the dense phase pulverized coal airflow to the pulverized coal mass flow rate in the primary air pulverized coal flow is 95%.
[0041] In this embodiment, through the control of the air volume, the concentration of the concentrated coal powder has a relatively high proportion, which is conducive to the formation of a rotating airflow in the center of the f...
PUM
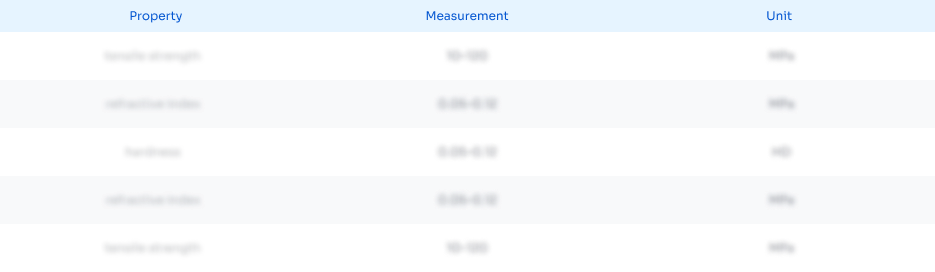
Abstract
Description
Claims
Application Information

- R&D
- Intellectual Property
- Life Sciences
- Materials
- Tech Scout
- Unparalleled Data Quality
- Higher Quality Content
- 60% Fewer Hallucinations
Browse by: Latest US Patents, China's latest patents, Technical Efficacy Thesaurus, Application Domain, Technology Topic, Popular Technical Reports.
© 2025 PatSnap. All rights reserved.Legal|Privacy policy|Modern Slavery Act Transparency Statement|Sitemap|About US| Contact US: help@patsnap.com