Modified polysiloxane and preparation method thereof and application of modified polysiloxane as foam stabilizer for flexible polyurethane foam
A polysiloxane and modification technology, which is applied in the field of silicone foam stabilizer for polyurethane foam, can solve the problems of discounted emulsification effect, general compatibility of raw material oil phase, etc., to avoid mutual influence and interference, and increase hydrophilicity Effect of lipophilicity on dimensionality, large structural space
- Summary
- Abstract
- Description
- Claims
- Application Information
AI Technical Summary
Problems solved by technology
Method used
Image
Examples
Embodiment 1
[0041]
[0042] Put 600 parts of terminal hydrogen-containing silicone oil with a hydrogen content of 0.1361% and a degree of polymerization of 20 (terminal hydrogen-containing silicone oil, manufacturer Hengyecheng Organic Silicon Co., Ltd.) into a 1L reactor, and heat it to 120°C under nitrogen protection to remove water Afterwards, cool down to 80°C, according to the total hydrogen content of terminal hydrogen-containing silicone oil (600 parts * 0.1361% = 0.8166mol): hexadiene: p-1-butenyltoluene molar ratio is (2:1:2) At 80°C, add 33 parts of hexadiene and 119 parts of p-1-butenyltoluene, mix well, and add 0.002 parts of Castel catalyst (3ppm) (Castel catalyst was purchased from Shanghai Sibao High-tech Co., Ltd. Material Co., Ltd. PL-56 manufacturer), the temperature of the system rose rapidly, and after the temperature stopped rising, polymer (3) with a molecular weight of 3600 was obtained after the temperature was kept at 110° C. for 30 minutes (measured according t...
Embodiment 2
[0046]
[0047] Put 600 parts of terminal hydrogen-containing silicone oil (manufacturer Hengyecheng Organic Silicon Co., Ltd.) with a hydrogen content of 0.0904% into a 1L reaction kettle, heat it to 120°C to remove water under nitrogen protection, and then cool it down to At 90°C, add 20 parts of hexadiene, 71 parts of p-1-butenyltoluene, after mixing evenly, add 0.003 parts of 5ppm Castel catalyst, the temperature of the system rises rapidly, after the temperature no longer rises, after 30min at 110°C, a polymer with a molecular weight of 5082 is obtained Compound (3) (determined by viscosity and GPC).
[0048] In this reactor, under nitrogen protection, 99 parts of tetramethylcyclotetrasiloxane were added according to the molar ratio of polymer (3): tetramethylcyclotetrasiloxane (1:2). Add 1.6 parts of catalyst trifluoromethanesulfonic acid, react at 50 DEG C for 6 hours, then neutralize and filter to obtain polymer (2), learn that its molecular weight is 5322, and its...
Embodiment 3
[0051]
[0052] Put 600 parts of terminal hydrogen-containing silicone oil (produced by Hengyecheng Silicone Co., Ltd.) with a terminal hydrogen content of 0.0541% into a 1L reactor and heat it to 120°C to remove water. Afterwards, cool down to 100°C, add butadiene at 100°C according to the molar ratio of the total hydrogen content of terminal hydrogen-containing silicone oil: butadiene: p-1-butenyltoluene (2:1:2) 8.7 parts of alkenes, 47 parts of p-1-butenyltoluene, after mixing evenly, add 0.003 parts of Castel catalyst 5ppm, the temperature of the system rises rapidly, and after the temperature no longer rises, it is obtained after holding at 120°C for 30min Polymer (3) with a molecular weight of 8014 (determined by viscosity).
[0053] In this reaction kettle, under nitrogen protection, 59 parts of tetramethylcyclotetrasiloxane were added according to the molar ratio of polymer (3): tetramethylcyclotetrasiloxane (1:3). Add 1.4 parts of catalyst trifluoromethanesulfonic...
PUM
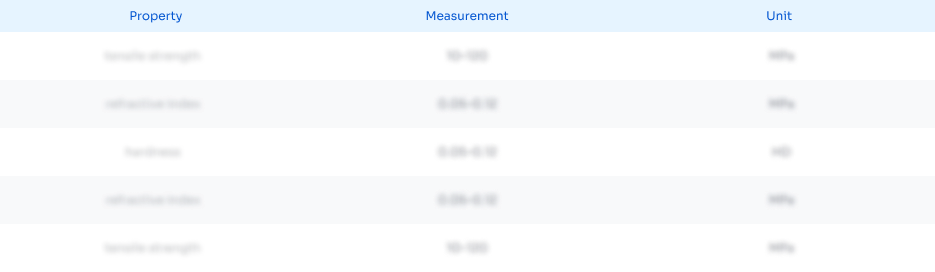
Abstract
Description
Claims
Application Information

- R&D Engineer
- R&D Manager
- IP Professional
- Industry Leading Data Capabilities
- Powerful AI technology
- Patent DNA Extraction
Browse by: Latest US Patents, China's latest patents, Technical Efficacy Thesaurus, Application Domain, Technology Topic, Popular Technical Reports.
© 2024 PatSnap. All rights reserved.Legal|Privacy policy|Modern Slavery Act Transparency Statement|Sitemap|About US| Contact US: help@patsnap.com